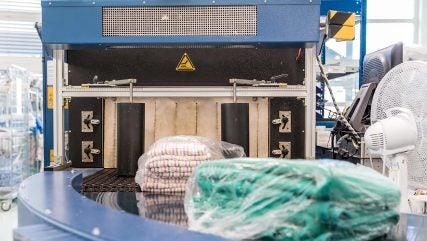
UK
Traditionally, clean linens for hospitality businesses have been protected by plastic covers, during transit from the laundry and while they are stored before being used. In recent years hospitality linen services have used 100 tonnes of plastics a week to protect clean textiles – of which only about 9% is recycled. With the drive to banish single-use plastic, finding sustainable alternatives has been a key objective for the Textile Services Association (TSA), UKHospitality (UKH) and the UK Housekeepers Association (UKHA).
In 2023 the three organisations along with its members agreed to work towards removing all single use plastic where possible from the processing of bed linens and towelling by 2025. It was described as an historic agreement – but an agreement is one thing, putting it into operation is quite another.
Recently the TSA conducted a survey of members to see how the plastic-free campaign was progressing. “The results are incredibly encouraging,” said David Stevens, CEO of the TSA. “Eighty-three per cent of respondents have started removing plastics from their operations – and nearly 40% say their delivery of hospitality linens is already plastic-free, including some of the biggest companies in the sector.” A further 5% said delivery would be plastic-free by the end of 2024, 17% by 2025, and the remainder by the end of 2026. It is estimated that up to 80% of single use plastics has already been taken out of the linen delivery system in the UK.
Stevens said: “Our research uncovered the unsustainable figure of 100 tonnes of plastic per week being used to wrap linen. Reducing this usage by 80% will save a staggering 12,480 tonnes of carbon emissions per year – and over 4,000 tonnes of plastic waste would no longer be going to landfill.”
Replacing plastics required planning and investment in alternative methods. These have included stacking linens direct into cages, using cage liners, and using hampers.
In some cases, it’s a huge challenge to eliminate the plastic cover. For example, it may be that the particular operation requires bundles of clean linens to be left outside temporarily, and a plastic wrap provides the most effective protection. And while hospitality is the prime focus for this initiative, there are other sectors that employ single use plastics for linen service, where the challenge will be greater. This is particularly the case where ensuring sterilisation is a critical issue, such as in the healthcare sector.
The survey results were presented during a round table meeting of laundry and hospitality organisations. One of the attendees was Premier Inn, which has been engaged in the programme to remove single-use plastic wrapping of hospitality linens for the past two years. The company’s procurement manager, Barnaby Mager, said: “It hasn’t been easy. We’ve worked in partnership with our laundry suppliers to overcome the operational issues and together we’ve achieved a 50% reduction so far. We are looking forward to improving this further. Premier Inn is hugely supportive of the progress being made across the industry.”
Center Parcs is also fully behind the industry’s move to find a sustainable solution. Samantha Stephenson, procurement manager said: “We are extremely keen to be involved in any initiatives to remove plastic, but it’s a challenging issue for holiday parks, when you are constantly dealing with the elements. We are currently in talks with all of our laundry partners to review our packaging and hope to go plastic free as soon as possible. In the meantime, we have established a collaboration with our linens wrap provider to bale, collect and closed loop recycle our linen and towel packaging.”
“There is a huge amount of support for this campaign across our industries,” said Stevens. “We’ve already made enormous progress, which is down to everyone involved being committed to the objectives. These are significant steps in the progress towards net zero.”