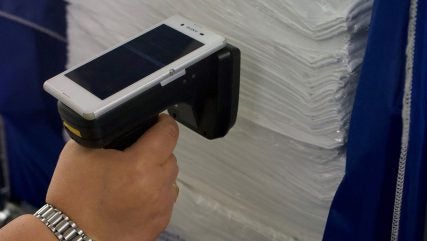
INTERNATIONAL
Dibella is making life easier for its textile service customers with a new service: on request, hotel textiles can be ordered with Datamars transponders directly ex-works. The chips are permanently available at the Dibella warehouse – the goods are delivered fully equipped.
To relieve its customers, Dibella now offers a new RFID-based laundry tracking service: On request, the company equips textiles ex works with LaundryChips (RFID tags), from Datamars (CH). Dibella is cooperating directly with the Swiss company for this unique service. Customers do not have to worry about ordering or providing the tags, thereby saving them time and effort.
“For years, we have offered our customers the option of inserting their own transponders into the laundry. We noticed that Datamars (CH), a pioneer in the field of industrially washable transponders, is used particularly frequently by our customers. The high quality and widespread use of Datamars tags worldwide have led us to enter into this cooperation and offer this new service,” said Simon Bartholomes, head of purchasing at Dibella.
Major cost advantage
This new system offers a significant cost advantage because: It is much more cost effective to send large batches of chips bundled together for production than to make hundreds of shipments per year for each individual order. Handling costs are increasing and shipping costs, especially overseas, have risen immensely. In addition, the customs authorities in some countries are very strict when it comes to importing chips, and this new system also minimizes the risk of customs-related delivery delays.
Transponder data as a future service
Another service is already in the pipeline: Dibella will soon offer the option of directly reading out the LaundryChips in its main warehouse and providing them as a CSV file together with the delivery note. This will eliminate the work step of scanning new goods for the textile service – when the goods arrive, the CSV file is simply entered into the system and can then be fed directly into the laundry cycle.
As there are different chip systems from company to company, this solution cannot be implemented directly for all textile service companies – but Dibella is happy to develop further for and with its customers, please contact us!
Benefits of RFID for laundries and their customers
The RFID technology not only improves efficiency, reduces losses and increases profitability in the laundry industrial process. RFID also improves the quality of service that the textile services can offer to their customers, thanks to a more efficient workflow and instant data exchange between textile services and their customers. No more worries or discussions about lost textiles: the customer knows exactly how many and which pieces have arrived/departed from/to the laundry. In this way, transparency with the customer is improved and invoicing can be based on reliable data. In addition, portable RFID readers allow for automated and quick daily inventory at the customer’s site to request clean textiles from the laundry on time.