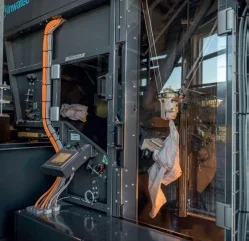
It is not easy finding suitable skilled workers, especially in the laundry industry. Automated systems provide the best way to combat this problem. With its smart machines and intelligent technology, Jensen is making laundries attractive places to work.
The shortage of skilled workers is one of the biggest challenges that businesses face today. The search for suitable employees can drag on with vacancies frequently remaining unfilled. When a company finally does find the right person, the risk of poaching from competition remains everpresent. This job seekers’ market can be costly for companies. Not only is searching for staff a time-consuming and expensive process, an understaffed team also has a long-term negative impact. Using stateof- the-art technology, Jensen is helping laundry companies all across the globe combat the shortage of skilled workers.
Humans and machines working hand-in-hand
“Work smarter, not harder” are wise words for laundries combating manpower challenges. When used in the right way, robots and similar machines make laundry operations safer, more efficient, and more self-contained – and laundries much more attractive places to work. When humans and machines work hand-in-hand in laundries, the staff enjoy the advantages of less physical strain, improved safety, and more fulfilling work. In fact, laundries that deploy intelligent automated systems benefit in four ways.
1. They become a more attractive place to work
Fewer repetitive tasks, improved safety, and a pleasant working environment: Intelligent automated systems make working in a laundry a more attractive prospect.
Safe sorting: The THOR sorting robot quite literally enables laundries to leave the handling of dirty linen to machines, which protect staff from hazards caused by possible contamination or injury from dangerous objects.
Ergonomic separation of clothing: The Viking separator separates individual pieces from the larger batch in a superfast, automatic process. It can handle even the heaviest batches without employees needing to strain themselves.
Flexible loading: The MetriQ loading station features various innovations to offer the ideal combination of ergonomics and efficiency. Different functions such as the flexible feeding height and “buttons to the front” function ease the burden of day-to-day work. The quiet design is also easier on the ears and the in-built lighting reduces the strain on the eyes.
Decentralised feed concept: The decentralised feeding concept of the Jenrail 2000 Automatic makes large-piece ironer lines safer. The relevant employees work from a distance, which prevents pit-related accidents and makes for a more pleasant working environment.
Lower ambient temperature: New technologies and improved insulation result in less radiant heat waste. This not only improves the energy footprint, it also lowers the operating temperature by several degrees, improving the working environment.
2. Streamlining
Here is a quick quiz question for you. In today’s most automated laundries, how many hands does an item of clothing pass through? The answer is, just six hands from three people – firstly in the sorting area when the bags of laundry end up on the conveyor belt, secondly at the MetriQ loading station, and thirdly at the packout station. This is possible because all the interfaces are automated.
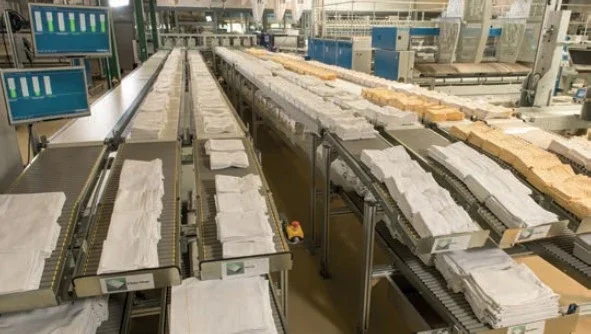
The BLIZZ robot feeds towels of different sizes into the Jensen Butterfly terry folder without any human intervention whatsoever. GREIT, the modular stack storage system for flatwork, links the folder with the logistics area. The intelligent Jenway transport and sorting system then handles the last mile of the automated solution.
3. Greater independence
With Laundry 2.0, there is no need to fear an understaffed workforce due to vacation, illness, or a lack of job applicants. The laundry can practically run by itself, being largely autonomous. The company depends less on personnel for day-today operations, putting it on more stable footing. Despite the large amount of stateof- the-art technology, Jensen’s solutions have been designed so that they can be operated without any special expertise.
If, however, a problem does occur or the manager is unavailable, staff can obtain help quickly and efficiently from the Jenassist remote access service. Maintenance contracts ensure the machines are serviced at regular intervals, which is one less thing for managers to worry about and they can focus fully on their core duties.
To ensure operations can continue seamlessly in an emergency, the online shop for spare parts is available 24/7 in many countries. As a further highlight, Jensen can also provide training sessions directly on site.
4. Digitalisation
Find out the facts with sound data: The comprehensive Globe by Gotli Labs data management system brings together data relating to the entire system and evaluates it in real time. All key operational information is just a click away, meaning laundries can see immediately what is working well and where things could be improved.
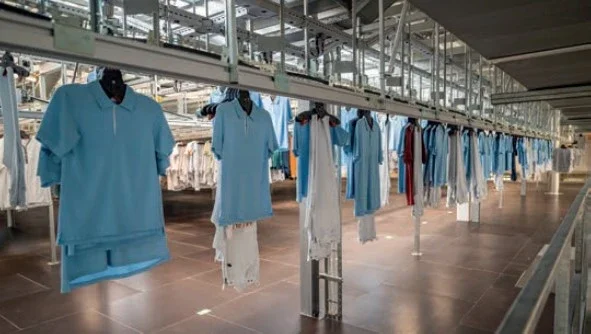
Globe is the most modern management tool for laundries in the world, keeping record of man and machine to assist management in making the right decisions at the right time. Globe is the innovative approach for central production monitoring that provides real-time information, allowing increased laundry productivity and giving peace of mind. It is the most complete production management system in the laundry industry, including staff scheduling, time and attendance, and a track-and-trace functionality.
Smart solutions and the internet of things are opening up great new perspectives for heavy-duty laundries. With the creation of Gotli Labs, a dedicated organisation with business experts, we are committed to the development of innovative new solutions for this industry.
Attract suitable skilled workers with technology
The laundry industry has entered a new era in which technology can take over most of the production process without human interaction, transitioning from an industry involving a lot of manual work to a place where fewer people work in more attractive and healthier workplaces. Jensen is continuously pioneering groundbreaking approaches, inventing and implementing radical innovations that automate the majority of laundry processes. Already six years ago, Jensen introduced the automation of the soil sort with robotics and AI through its partner Inwatec – with a tremendous impact on the laundries’ profitability and sustainability. Utilising robots to outsource strenuous work and repetitive tasks has numerous sustainable benefits: a safer, more pleasant work environment, reduced energy consumption thanks to an optimised workflow and production optimisation, plus extended lifespans of textiles and equipment that do not get damaged by unwanted objects.
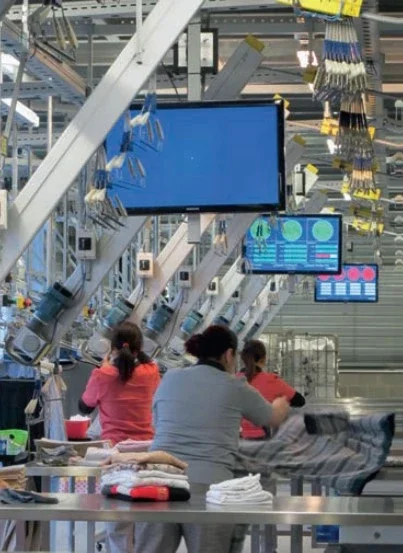
More attractive, efficient, autonomous, sustainable, and digital – when a laundry embraces automation in all areas, the benefits are clear. Automation makes Laundry 2.0 an innovative workplace where talented staff actively help shape the future and add value. After all, one thing is clear: We are merely at the start of an extremely exciting development.