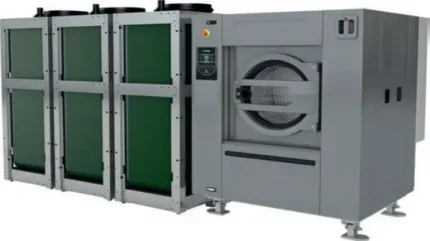
Heavy duty dryers are massive both literally and figuratively in the linen rental market. With these big fellas, energy costs are of course a major factor nowadays globally, so any developments that cut time, energy use and can make the bottom line more black than red for hard-pressed operators is welcome news.
Is steam generation still necessary? Do we still need dryers for bed linen when water extraction is so good at washer level linen can go straight to the ironer line? Do we just need them for fluffy towels nowadays? We got answers from the big players in the market.
Eduard Colomer, export manager at Domus says: “We know how important it is to have efficient machinery. This has always been a request from industrial laundries managers and owners running businesses where efficiency and production costs are the most important points, especially in the last few years, and we like to listen to them and give them what they are looking for.
“For this reason, at Domus we like to explain the high efficiency of our products: low water and chemical consumption and great energy savings throughout their lifespan. And how do we do that? It is not a simple statement, but differently from other brands, we supply numbers and figures. We even send a leaflet and a real calculator to them.
“You can see our calculator videos, for example this one where we show clients that a Domus 60kg gas dryer can save 121.000 kW a year, thanks to the Air recovery system, thermal insulation, and intelligent moisture sensor.” https:// youtu.be/Rb423CxlN2Y
Colome continues: “Most big facilities still use steam as a heating option, so we sell a lot of steam dryers. However, in new facilities the tendency is to install gas, as this is a cheaper option in terms of installation and maintenance.
“When we prepared some efficiency videos with specific figures of savings, we use gas heated dryers: DOMUS big capacity tumble dryers for example, (35 – 45- 60 and 80kg) come in different ranges, and the most efficient one is ECO-ENERGY: Eco-Energy industrial dryers have a wide variety of standard features that contribute to optimise consumption and achieve greater energy savings in the laundry. When you explain these real features and show the numbers, clients get really interested,” says Colomer.
Drum roll
For example, he cites Domus Efficient Dry intelligent humidity control, which adapts the drum rotation speed to the humidity level in each drying phase. This can give a saving of 5% power for example in a 60kg gas dryer. It may not seem much but for a laundry working 300 days a year, in one year the saving is considerable, watch the video for the example: https://youtu.be/ Re8vFrwwhF4 Domus also has a new automatic sliding door that was developed recently to help ergonomics, comfort of operation and https://youtu.be/dT7ie- 87O_w
Colomer says that dryers are not much used to dry bed linen, “at least when we visit laundries and show them the Domus high spin washers (from 35kg to 120kg) with efficient features and the ECOTANK XL (water recovery tank) they use the high spin washers with it, saving enormous amounts of water (watch this video of water recovery https://youtu. be/E-3A6wjD4zE (to see how much water and energy they can save with 3* 80kg Domus washers)”.
“The advantage is that the bedlinen can go straight to the ironers, of course it will depend on the type of ironer they have, but a dryer is hardly ever used. Our export sales team and dealers are really happy to explain these features, as these are key arguments that help laundry managers decide for a machine change or investment,” says Colomer.
Energy costs
Meanwhile, Jensen, in an environment of increasing energy costs and wages, compounding competitive pressure and decreasing margins, says today‘s laundries face enormous challenges which must be met with comprehensive measures to increase efficiency. One of the primary goals of Jensen’‘s product development is to increase the efficiency and productivity of laundry systems as a whole. The new XR dryer is designed to help laundries achieve their business goals.
Jensen’s new XR dryer was a crowd puller at the Clean Show 2022 in Atlanta and the ExpoDetergo 2022 in Milan: Big volumes require big machines. The XR dryer will process big cakes with a diameter of 1300 mm/51 inches. The wider opening also allows faster unloading, with savings of 10-20 seconds per batch: Laundries can process more loads within one shift thanks to the new AirWave feature. AirWave also speeds up the subsequent finishing process with its unique blow-out, reducing tangling of linen. The new XFlow feature ensures a 10-15% higher evaporation capacity and optimizes the heat distribution for an even and fast drying process. Thanks to the new perforation pattern of the drum the air flow increases by an amazing 20%.
The XR’s precise and well-dosed heat control, InfraCare, reduces the energy consumption and the drying time, while extending the lifetime of the linen. The control detects varying weights and residual moisture, and avoids unnecessary energy supply and long drying times.
Optimal air management
The new horizontal fan unit together with an optimised drum geometry, a new perforation pattern and the new front air channel improve the air flow and the heat distribution by an amazing 20%. This ensures an outstanding energy balance and consistent, reproducible perfect drying results. The new XFlow ensures a 10–15% higher evaporation capacity by producing an optimized air flow through new front air channels.
The frequency controller for the fans and the individual, process-based control of air volume guarantees extremely low wear operation of the fan motors.
The new automatically controlled circulation flap continuously regulates the optimal ratio between the fresh air and the circulating air depending on the degree of dryness of the goods and the individually adjusted program. As a result, the highest measure of efficiency is assured. In addition, XR dryers are very well sealed, which prevents escaping air. The outstanding insulation also assures low heat emission and a low noise level.
Gentle laundry handling
Laundries can process more loads within one shift thanks to the new AirWave feature, says Jensen.. AirWave also speeds up the subsequent finishing process with its unique blow-out, reducing tangling of linen. The large drum diameter enables an optimal fall curve and guarantees an outstanding air flow through the linen. The blow-out unloads the linen very quickly with a nice and fluffy result so that finishing quality is improved considerably by preventing wrinkling and tangling. The wider unloading opening adapts perfectly to the following conveyor widths of either 800 or 1000mm (31 or 39 “).
Due to the frequency control of the drive motor, custom adjustments of the drum speed for different types of linen and drying processes is possible. Comprehensive technology with finelytuned, sophisticated software regulates and monitors the drying process.
The new Xpert in drying
The XR series represents a new era in efficient drying in laundries: The latest technologies in combination with numerous innovations assures an efficient machine concept. The new XR dryer is designed to help laundries achieve their business goals.Drying has never been so efficient, environmentally-friendly and powerful.
Jim Shaw, vice president and national accounts sales manager for Lavatec Laundry Technology has plenty to say on the subject and gives an isght on how the large niorth American linen rental businesses are playing their hands when it comes to dryers.
“Relative to heavy duty commercial dryers, the preferred energy source used for drying in the US is natural gas. This is for several reasons, including the cost of energy, speed of production, and energy availability.”
As for whether we still need dryers for bed linen when water extraction is so good, here, Shaw concurs with Domus’ Colomner’s assessment: “No, not all. There are several critical factors used to determine whether or not bed linen can go directly to the flatwork ironer after extraction.
“Textile construction involves the thread blend (poly/cotton), count and hemmed layers. The moisture content is what remains in the textiles after extraction; the preferred level is in the mid 30% range or less. And the preferred ironing system would be a chest type with a vacuum.
“Well maintained steam or gas heated thermal oil energy sources will suffice, with the size and operating speed of which will be impacted by the prior conditions as noted.”
Shaw addresses towels processing in dryers saying: ““The primary function of dryers is to remove moisture after the wash process. Creating fluffy, soft towels is more related to temperature and air flow in the drying process. Higher temperatures will dry the textiles faster, but it can cause the cotton loops of the towels to become over dried and rough while trying to dry the webbing the loops they are tied to. Lower temperatures will result in softer towels, but the tradeoff is it will extend the drying and turnaround times.”
At the Clean Show in Atlanta last year, Lavatec showed its truly revolutionary LAVACascade drying system, alongside the LAVAPress ULTRA 597S 60-bar extraction press, a system so massive there is nothing else in the marketplace that rivals it, says the company. Lavatec president Mark Thrasher remarked at the time: “We introduced LAVACascade a year ago (2021), (See https://www. laundryandcleaningnews.com/ features/featurecascading-energysavings- 8653403/) and now we have this opportunity to showcase it with LAVAPress ULTRA. Both machines are a result of listening to our customers, what strategic objectives they were pursuing, and the equipment they need to achieve their goals. Most of these discussions focused on energy conservation and plant efficiency. Together with our tunnel washers and other results-based equipment, we have a complete solution to help any laundry operator succeed.”
Powering up
Kannegiesser has big claims for its latest dryer technology, saying: “Technology and innovation make the difference. A difference that our customers should be able to see and feel first hand. As for our transfer dryer PowerDry, the difference is called CareDry and Eco2Power.
“CareDry is a special drying program that reliably preserves the quality of terry cloth. It prevents overdrying and thus scorching and greying of the textile fibres. CareDry meets the highest requirements for softness, whiteness or colour-retaining.
“Eco2Power is a process control that combines lowest energy consumption with maximum performance. Due to the optimal use of circulating air, less heat supply and thus energy is required. At the same time, the automatic control system reduces process times and allows greater performance.
Towelling dry
The PowerDry batch dryer provides a special drying program developed for high quality processing of terry cloth: the CareDry process.
Terry is built up from a firm ground fabric usually woven in warp and weft. This ground fabric holds the loop texture which forms the typical structure of the terry surface.
In the drying process, moisture has to be removed from the ground fabric as well as from the loop texture. It is easy to imagine that the tops of the loops dry fastest as they are directly exposed to the drying air. When the loop tops are already dry, there is still moisture in the deeper sections of the terry cloth.
The loops are drying faster than the moisture can move up from the terry inside. This can lead to overdrying of the loops, with the danger of scorched loop tops and destroyed colours. Unfortunately, it is mainly the outer loop texture which is responsible for the feel (haptics) and the visual impression of the entire terry cloth.
The laundry can resolve this problem by choosing the CareDry drying program in the PowerDry. The drying parameters of the CareDry process compared to the standard terry process.
The inlet air temperature as well as the drying temperature are significantly lower with the CareDry process. This creates more time for moving the moisture from the ground fabric up to the loop texture where it can evaporate to the drying air. The energy consumption decreases. However, the total process time slightly increases.
It is not necessary to choose the CareDry process in general for all terry cloth, as the standard terry drying process is already optimized for this type of textiles. But especially for very thick articles and such with special high demands on softness, whiteness or color-retaining, the CareDry process can lead to a significant higher quality in the drying process of terry cloth.
Low energy, max performance
Innovative process control and heating management methods secure a low energy consumption of 1.1 kWh/ltr evaporated water, while shortening overall process times. Together, they make the PowerDry the most efficient transfer dryer on the market.
With the continuous measurement of the item’s temperature via InfraTouch, together with supply air and exhaust air temperature, optimal process settings are realised at all times within the control circuit. This results in maximum circulation rates and ideal conditions for the laundry in the inner drum.
The higher the air recirculation in the process, the lower will be the heat demand supplied by the heating element. On the one hand, this results in huge energy savings. On the other, the exact degree of drying can be stipulated at any time. This leads to the precise detection of the dry point.
The core properties of the ECO2power option are:
- Low required energy supply
- High air recirculation proportion
- Optimal laundry fall curve
- Exact dry-point recognition