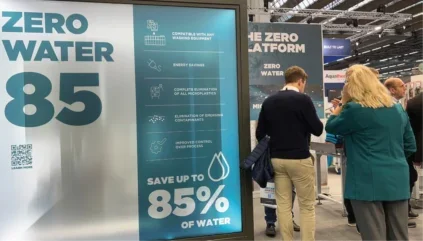
Where better to look for energy saving breakthroughs than Texcare 2024 which was flagged as the Mecca for the topics that are driving the industry such as hygiene, automation, digitalisation, logistics and AI. Piut them all together and you have the perfect recipe to create an energy saving laundry.
Wolfgang Marzin, president and chief executive officer (CEO) of Messe Frankfurt believes the industry is meeting the challenges of labour shortages and rising energy prices with a significant surge in innovation. The solutions are available, as demonstrated by the exhibitors with their machines, technologies and expertise. The leap towards robotisation was clearly visible at the stands. The circular economy was also in focus: many innovations showed how machine builders and textile manufacturers are working together to advance sustainability. Texcare provided the right impulse for companies in the textile care industry at the right time, enabling them to secure their successful market position by investing.
Andreas Schumacher, general manager of the German Textile Care Association, one of the partner industry associations, alongside German trade association VDMA Textile Care, Fabric and Leather Technologies, summarised: “There was a sense of a fresh start. You could feel that after eight long years, the exhibitors were eager to show their products and developments, and the visitors were excited about innovations. In particular, the topics of automation and digital solutions, as well as robotics, were the subject of much discussion, as many companies are facing a shortage of skilled workers. After the pandemic and the energy crisis, the discussions were once again characterised by a willingness to invest and a sense of optimism.
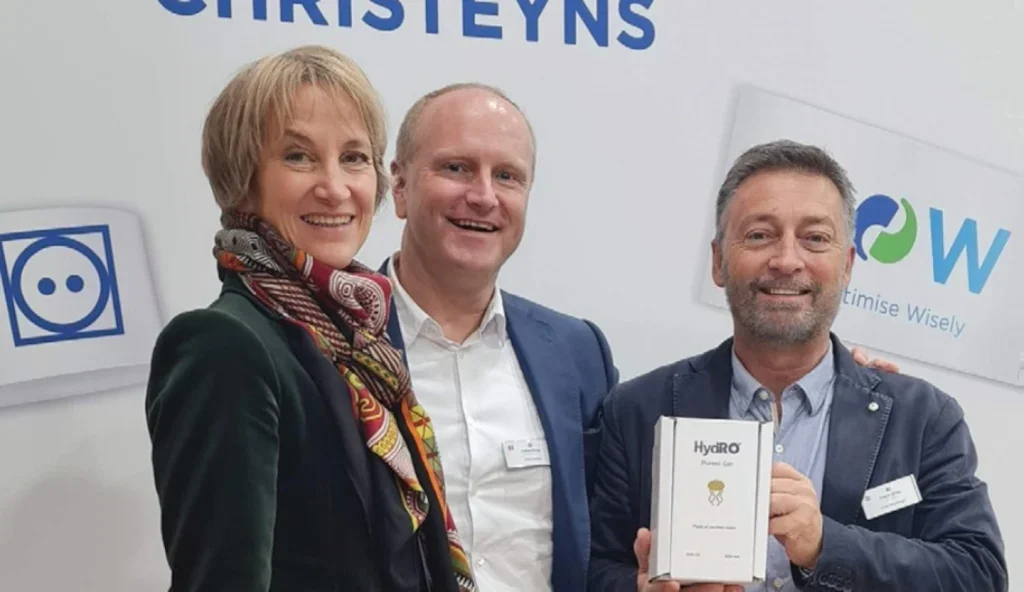
“Energy costs and corresponding opportunities for saving energy and other resources were also a key topic. Last but not least, companies in the industry are working to further improve their circular business models and to adapt to the upcoming regulations for the recycling of textiles.”
There were many examples of utilities shaving but one of the most eye-catching was Christeyn’s which showcased its EPIC system, powered by enzyme technology, which helps laundries meet strict environmental regulations while reducing wastewater costs. Complementing this is the HydRO water treatment and recovery technology, developed in partnership with Veride. With more than 30 systems installed across Europe, HydRO enables clients to recycle at least 80% of their process water, resulting in a savings of over 100 million litres in 2023 alone. Plans for 2024 aimed to double this impact. It is with this recycled and purified laundry water that Christeyn’s HydRO Gin is made. Now there’s a bonus.
At Domus, DomusConnect IoT technology (connecting everyday devices to the internet) allows Domus machines to connect online, gathering key data to improve washing and drying times while managing the business remotely. This gives users more control, offering detailed reports on production, cycles, consumption, revenue, and more. It also ensures high-quality processes, guaranteeing hygiene and disinfection in every wash and dry cycle. “Additionally, our new LEMS (Laundry Efficiency Management System) collects data from various counters and centralises it, generating useful metrics for industrial or self-service laundries. Once the data is gathered, it is transmitted via IoT to DomusConnect. The LEMS system enables real-time tracking of water, gas, and electricity usage, and creates detailed, custom reports through DomusConnect. With this system, Domus shows its commitment to innovation and efficiency, providing a complete solution that turns your laundry into an Ecosmart laundry,” said Andreu Arrom, Latin and Spanish laundry director at Domus. Meanwhile he Ecotank XL water recovery systems are perfect for front-loading washers as well as sanitary barrier washers as they help create a more sustainable and efficient laundry, allowing water recovery and promoting environmental care.
The Jensen booth was packed with plenty of innovations for its many visitors to inspect, including advances in laundry automation, robotics, chemical free wash disinfection, a new super-efficient mechanical handling system and a highspeed garment loader along with other new equipment and solutions. The solutions on the stand fully supported Jensen’s avowed mission to, along with laundry businesses, create the future of laundry automation and shape the industry in a sustainable way.
Girbau’s Zero Water solutions allow the recovery of up to 85% of water, saving money, guaranteeing efficiency, and actively contributing to the environmental protection.
Also attracting attention was the new PRT60 turbo press which can process up to 2,400 kg of linen per hour thanks to its turbo cycle time of just 60 seconds combined with a 30-second press time. By increasing pressing time to extract more water and reduce drying time, launderers can save up to 2.5 kWh per batch of linen.
Responding to the growing demand for automation as a solution to labour shortages and the need for efficient production processes, Kannegiesser unveiled new automation and robotics solutions, enhancing productivity across laundry operations. As Kannegiesser’s Jennifer Frentrup told LCNi: “Robots are great for productivity and for tackling the labour shortage. They don’t need to go to lunch or have coffee breaks – they have no natural bodily functions to attend to. All they require is some occasional maintenance.” LCNi looked at the new EMR SynchroRemote feeder which Kannegiesser says offers 37% more feeding capacity than conventional feeders and 66% less grip needed on the sheet, therefore 25% less risk of wrist injuries as there is less physical stress when loading the item. The X-Stream tunnel finisher has four modules in three, offering super efficiency. The new counterflow design saves time and energy. It works by juxtaposing cold and heat. The items enter from the hottest end taking heat with them in the counterflow to the coldest point. It is a very efficient system.
Biko and Laundry Robotics drew a big crowd keen to watch the antics of Laura, Robin and a new addition to the family, Roger, on all four days of the show.
With Roger, Laundry Robotics has expanded its product line of automatic towel feeders to three market leading models. “Laundries have different kinds of requirements for their towel folding, therefore it was only logical that we expand the range to offer even more possibilities and solutions,” says Erwin Maassen, one of the company founders.
With this new addition, Laundry Robotics believes it can fulfil almost every need of a laundry for automatic towel feeding.