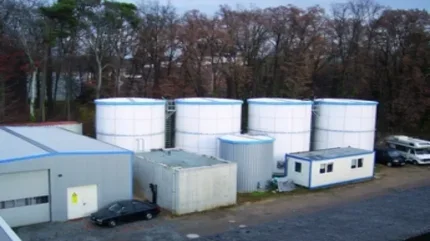
Countering the rising cost of laundry effluent has become a priority for the industry from both an economic and environmental viewpoint.
Laundries, especially industrial laundries, still dump a huge amount of waste-water into the sewer, even though many have cut their water consumption considerably.
Textil-Service Klingelmeyer in Darmstadt has been involved in a project to develop a water recycling system since the mid 1990s when the price of fresh water, and especially waste-water, in the region increased enormously. For this reason Günter Klingelmeyer, the laundry’s owner/manager, decided to develop a process that would achieve almost complete water re-use. Such a system would contribute to sustainable, economic water management as well as reducing reliance on municipal treatment.
The result was the LIWATEC (Laundry Innovative Waste-water Recycling Technology) project, a venture involving the Klingelmeyer laundry, the University of Applied Sciences in Karlsruhe, Germany, and the TU-Darmstadt, Germany. It was funded by the EU (as part of the LIFE-Environment programme) by the federal state Hesse and by the city of Darmstadt.
Work to develop the basic technology started in 1997 with the University of Applied Sciences in Karlsruhe under the support of Professor Dr Jan Hoinkis. The early stages included a pilot at the university, using a domestic washer, which had a capacity of 200litres/day. A larger installation handling 10m³/day was then established at Klingelmeyer laundry. Then in December 2004, the project started to lay the foundations for building an industrial system at the laundry.
In 2006, a recycling plant with secondary water treatment was built at the laundry. The plant included a machine hall, a 125m³ bioreactor, a tunnel linking to the laundry, four 200m³ tanks and one tank of 50m². Membrane cartridges with 460m² membrane-area were submerged in the bioreactor, which clarifies 200m³ waste-water per day.
The COD-value is reduced about 90-95% and never exceeds a value of 70mg per litre. The low-pressure reverse osmosis disposed downstream has a capacity of 200m³/day.
The plant has been fully operational since October 2006. Currently the laundry, which employs around 100 people, handles around 15t linen/day.
The recycling plant is reducing the laundry’s consumption of fresh water from the municipal system to around 35% of the total (including water for the steam boiler, toilets and cooking).
The washing machines produce about 150m³ waste-water/day and the plant now recycles around 80% of this (currently 81.3%). If rainwater is included, the quote is considerable higher.
The laundry estimates that it can reach its goal of recycling 90% within six months, though this depends on several factors such as the carbonate water hardness.
How the system works
The recycling plant treats the water in two stages and allows the water to be used in the washing process.
The first stage is a coarse filter that traps suspended particles. The waste-water is then stored in tanks that are sufficiently large to hold the water from two days’ production. The water is sent from these tanks to the membrane bioreactors (MBR), where the main cleaning takes place.
Air is injected into the reactor to scour the membranes and to drive the biological treatment. Micro-organisms eliminate the biodegradable elements in the water.
The purified waste-water is filtered through membranes with a pore size of average 0.4 µm, and subsequently collected in the washing-water tank. So the micro-organisms remain in the bioreactor.
The advantage of this system, compared with conventional sewage technology, is that the specialist micro-organisms establish themselves permanently in the system, and this leads to more efficient purification.
After micro-filtration, the clear water from the permeate, which has considerably fewer microbes, can be used directly in the washing process.The other part of the permeate is further treated in the low-pressure reverse osmosis unit with spiral wound modules to retain salts. It can then be used as high quality water, primarily in the rinse.
The integrated process generates two kind of waste for disposal.
The surplus sludge is stored in a separate tank and is collected by commercial waste management enterprises.
The concentrate from the reverse osmosis treatment is drained to the municipal treatment plant. Water losses resulting from water treatment and washing processes are replaced as far as possible by rain water.
Waste-water recycling has many advantages and the Klingelmeyer laundry says that the project has provided an easy to use and cost efficient system that is modular in structure and can therefore be adapted to differing laundry requirements.
The recycling plant offers an almost closed process water cycle that allows re-use of up to 90% of waste-water.
The washing process has been tested with a range of chemicals and the results are good, and finally the system minimises environmentally critical waste effluent.
As the next stage, the LIWATEC system could be made available commercially and Klingelmeyer is seeking other laundries that might be interested in such an installation.
Companies supplying the project include: Kubota Deutschland – bioreactor membranes; KBU – storage tanks; Endress & Hauser Messtechnic – most sensors; Vipa – program control; Siemens – process control; and Frank – piping.