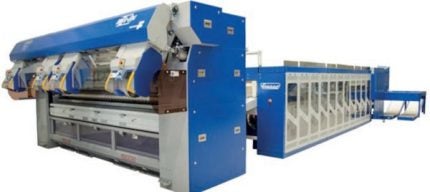
We are far enough down the line now, says Lapauw, to see some particular trends in the post- Covid laundry market. “First of all,” says marketing manager Wim Demeyer, “we see that the market for chest heated ironers is picking up rapidly. As tourism is already surpassing pre-Covid levels, laundries need higher production capacities and the small, commercial laundries are rapidly ‘growing out’ of their roll-heated ironers, replacing them with a single roll chest ironer with folder. Here, Lapauw offers a wide range, from 800 mm diameter up to 1600 mm roll diameter, while the flexible chest technology combines efficiency with a high quality finish.
“Needless to say, spiralling energy costs are still an issue. The IronMAX is the latest generation 2-roll and 3-roll diameter 1200 mm ironer. With features like a heated bridge that spans more than 1 metre, the individual Lapauw spring technology and true parallel circuit for the thermal oil (gas heated versions) and steam (steam heated versions), the IronMAX is one of the most efficient ironers in the industry, offering an energy consumption of lower than 0,9 kWh/kg removed water.”
Demeyer also points out: “Next to increased demand for production capacity, the post-Covid world sees another issue – increased cost of personnel and difficulties to find and retain staff. This prompts the laundries to put their efforts on automatisation and look for smart feeding and folding solutions.”
However, Lapauw beielves it has the solution. “Together with the Japanese manufacturer, TOTO, Lapauw offers a wide range of feeding and folding solutions, among them the VS-line folding equipment.
The VS folders are large piece folders which have 3 to 5 individual stackers that are positioned inside of the footprint. This not only allows you to save valuable space (no stackers on the side) but also to already sort the folded linen to size, which reduces the workload of the personnel in the finishing and expedition departments. And, addsDemeyer: “ We also offer centralised conveyors.”
Flexible choices
Jensen, meanwhile, also offers a wide range of heavy-duty ironers covering all needs within industrial laundries. The Jensen ironers can be divided into two groups: Ironers with fixed chest and ironers with flexible chests.When looking at the advantages of the flexible chest ironers, they have a higher evaporation capacity over time compared to a conventional fixed chest ironer of same size and diameter. This is because the flexible chest adapts to the reduced roll diameter whereas a fixed chest ironer loses contact to the roll over time. The extra capacity of a flexible chest ironer can be significant depending on the condition of the padding of the fix chest ironer at the time of comparing.
Jensen supplies ironers to laundries that want the productivity of the flexible chest combined with the advantage of a thick chest. Jensen’s´s response to that is the newly developed Kalor ironer range incorporating a semi-flexible chest with a thick inner plate of 8 mm, which is double thickness compared to the inner plate of the flexible chest used on the wellproven EXP and EXPG ironers. With this sustainable approach, laundries can extend the lifetime of the chest because deep scratches coming from, for example, steel buttons can easily be repaired.
So, what are these industrial strength ironers made of? Jensen has always used carbon steel material for its ironers as it outperforms stainless steel when it comes to flexibility, and the low friction reduces the risk to pleated linen and increases the lifetime of both linen and padding. It also multiplies the heat conduction by a factor of four. Finally, the new flexible chest incorporates bigger flow channels and thicker material.
Depending on the type of heating source, Jensen ironers come as steam, or self-contained thermal heated gas ironers. The EXPG and Kalor gas ironers use oil as the heating medium and are supplied with an integrated heat exchanger and a gas burner to heat the oil. “Thanks to a new design of the heat exchanger and optimum control of the burner, the Jensen gas ironer was elected ‘best-in-class’ by a customers operating gas ironers of various brands,” says Nicolas Gostony, marketing and sales at Jensen.”Furthermore, the self-contained gas ironer allows running extra hours without steam supply, thus you can shut down the steam boiler and continue ironing the flatwork after hours, which also saves energy.
“Finally, an optional integrated nitrogen blanketing system prolongs the lifetime of the heat oil thus reducing the oil changes and is recommended for laundries running three-shifts.”
Gostony explains that because the production of textiles requires a lot of energy and replacing them is expensive for the laundries, it is crucial to ensure gentle treatment of the linen during the ironing process. Thanks to higher evaporation capacity of the Jensen flexchest ironers, laundries can prolong linen lifetime by reducing the ironing temperature or the roller pressure without reducing capacity.
Just as the ‘Sinner’s Circle’ describes the main components of the ideal washing process, the ‘JenFin Circle’ (see illustration above, left) illustrates the four major variables of the ironing process that may impact linen lifetime: temperature, time, pressure, and friction. These four variables need to be applied in the best way to achieve great finishing results coupled with higher productivity to reduce the effect of linen wear and distortion. “Most of all linen damages happens in the ironer, especially when processing blended textiles that have become very popular. That’s why the JenFin Circle is so vital to consider as part of all commercial and sustainability processes,” says Gostony.
Heating band technology
Kannegiesser says that its latest heating band technology ensures high performance, excellent ironing quality and fast temperature adjustments to the textile requirements. The HPM ironer series combines a multitude of advantages, says the company. “Added to this are the enormous energy savings compared to conventional ironer chests. Given current energy costs, the savings with Kannegiesser heating band technology can quickly amount to fivedigit amounts per year in single-shift operation,: says Michael Harre, head of Kannegiesser’s sales and marketing team.
He explains: “Due to the special geometry of the stainless steel heating band, an HPM 2-roller ironer, for example, provides the same evaporation performance as a conventional 3-roller ironer of the same diameter. This means significantly less mass that must be heated up in the morning, as well as less heat radiation and less condensate loss during operation.”
Below you will find the calculation of these savings based on 250 working days per year in single shift operation:
Heating up
With a working width of 3,500 mm, the heating band of the HPM 2-roller ironer weighs around 5.2 tons less than the rigid trough of the conventional 3-roller ironer.
With HPM, this amount of steel needs to be heated up less in the morning. You can roughly calculate that 43 kg of steam is required to heat 1 tonne of steel from 12°C to 192°C. With 250 working days per year, the savings for heating up in the morning with the HPM add up to around 46,000 kWh per year.
Heat radiation during operation
Due to the smaller surface area of the heating band, the HPM 2-roller ironer has around 15 kW less heat radiation during operation than the conventional 3-roller ironer. Here, with 2,000 operating hours in single-shift operation, around 30,000 kWh are saved per year.
Condensate losses
The lower steam consumption and the shorter ironing surface of the HPM 2-roller ironer compared to the conventional 3-roller ironer also lead to significantly fewer condensate losses. Therefore, the losses through the steam trap of the HPM is around 16 kg/h lower than with the conventional ironer. Extrapolated over the year, the energy savings due to the lower condensate losses amount to around 26,000 kWh.
“The heating band technology saves over 100,000 kWh per year in single-shift operation thanks to the faster heating up in the morning, the lower heat radiation during ongoing operation and the lower condensate losses. At current energy costs that’s at least £10,000. In addition, around 20 tons less CO2 is released annually in single-shift operation. Thus, the HPM is truly a guarantor for energy savings,” says Harre.