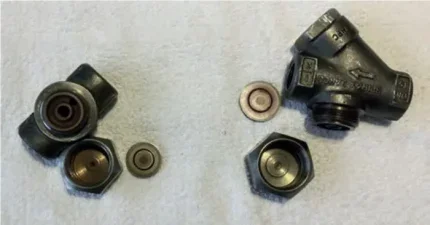
As we start the new year with the seasonal downturn to cope with, to say nothing of the massive increases in the cost of gas and electricity, some high street cleaners will be faced with a possibly a greater threat to their survival than in the pandemic. Hopefully, the coming year may bring some relief in the cost of gas and electricity but in the meantime it is possible that with little cost in terms of time and materials many cleaners could benefit from substantial reductions immediately. There are, of course, some fairly obvious areas where savings can be made, for example:
Turning off lighting when not required.
Extending service times to allow optimum machine and equipment utilisation.
Operating the machine and finishing equipment say three or four days a week.
Maintaining steam pipe lagging in good condition and ensuring that there are no gaps.
Typically an unlagged ½” steam pipe at 5bar pressure will give off around 190 watts per metre per hour. If the boiler is on 8 hours a day, 5 days a week, 52 weeks a year this is 395,200 watts (395.2 kilowatts) At 50p a kilowatt = £197.60 a year. That is lmost £200 for every metre every year. This means that even rightangle bends are worth protecting. There is however one, not so obvious area where there are potential and substantial savings to be made.
Steam traps
Steam traps are those hidden away unseen devices that clear away condensate from our presses, rotor cabinets, ironing tables and other types of steam equipment. They are normally reliable and for the most part give very little trouble. However, it is only when a piece of equipment starts to cool down, the boiler feed tank gets much hotter than normal or clouds of steam start to appear from the drains at the back of the unit that staff begin to realise that things are not what they should be and start to investigate. In the worst case nothing is done until a large unexpected increase in gas or electric usage starts the ball rolling.
There are various types of steam trap in use but in unit shops but the most common is what is the thermodynamic trap usually referred to as a TD trap. It is not uncommon to find that in larger installations more than one type of TD trap is fitted but all have a similar appearance. In the case of drycleaning machines or ironers fed from a central boiler, higher capacity bucket traps may be fitted. When trouble starts it is usually due to debris or rust in the system causing a blockage or the disc to stick in a TD trap preventing the release of condensate or allowing the release of steam. In the case of bucket traps dirt in the system can cause the float to stick, but generally bucket traps function more reliably than the TD type which some engineers have found work more reliably if installed upside down.
Top tip
In the case of TD traps, if things start to go wrong a quick, but sometimes temporary solution to the problem is to tap the offending trap sharply with a light hammer/medium hammer. This shocks the trap and the disc inside and usually releases the blockage or the disc and the trap then continues to function normally. In some cases this may also work for bucket traps by releasing a stuck float mechanism.
Finally, live steam is extremely dangerous, so do not attempt to dismantle steam fittings unless you have some experience in mechanics or have experience working with steam and never ever work on equipment unless it is completely cold.