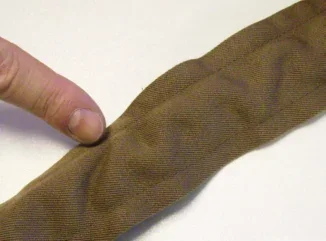
Designers are constantly seeking different effects and styles and inevitably new fabrics and finishes. This is bringing a whole new range of problems for drycleaners, along with some familiar old ones.
Labelling is not improving, so it is wise not to rely on the care label if gut instinct and twenty years’ experience sounds a warning. It is often the hidden components which give the most problems, such as interlinings which shrink excessively (leading to rippling) or padded garments which will not dry (because the outer fabric is impermeable not only to wind and rain but also to the drycleaning solvent, which is trying to evaporate from the inside during the drying stage).
Drycleaning skills cannot be neglected, especially when stain and soil removal skills are needed to remove collar grime, or the appropriate program needs to be selected to ensure drying temperatures are correct to avoid damaging modacrylic fur linings. Pressing still catches out not only the untrained amateur but also the hardened professional, snatching defeat from the jaws of success when a perfectly cleaned garment is destroyed at the finishing table.
Manufacturers continue to make cleaners’ lives quite unnecessarily difficult. There is now a suite of modern revised standards for checking garment care labels. This starts with a systematic method for assessing performance (reference 1), which includes shrinkage, colour change, trim damage and other factors which feature daily in complaints to drycleaners. Part 2 of the suite gives the correct method of test using perc (reference 2), Part 3 covers hydrocarbon and Part 4 covers wetcleaning. There is even a procedure for dibutoxymethane (Solvon K4) in Part 5 (reference 3).
This means that there is absolutely no excuse for manufacturers not to properly check drycleanability and wetcleanability when launching a new garment range. Yet even some of the most advanced importers of garments into the UK, Europe and the US persist in labelling by guesswork. There are a few who believe, mistakenly, that it is sufficient to send a test garment out to a local cleaner in the country of manufacture, and if this comes back undamaged, it is taken as proof of cleanability! The International Standards Organization (ISO) is a highly reputable body, whose members comprise most national standards organizations worldwide. All of the major trading nations with which the UK has dealings support ISO standards, yet its work for the clothing industry and for the cleaning sector appears to be going to waste and is being ignored! It is the cleaner and the consumer who are suffering from this. Perhaps this is one area where common sense needs to be given a spur by political action, by the UK government in parallel with the EU and other trading blocs. This month we look at just a few of the surging problems that are emerging with outer coats.
Belt distorts when cleaned in perchloroethylene
Fault: after drycleaning on a delicate cycle much of this belt came out severely rippled and distorted.
Technical cause: the problem here lies with the Internal stiffener for the belt used by the manufacturer. The outer fabric is fine, but to be drycleanable, all of the components must be able to withstand a full drycleaning process in the solvents allowed by the label. The belt interlining is designed to give body and support to the belt, but this belt shrank and became distorted in the presence of the solvent despite the garment being labelled with .
Responsibility: the manufacturer should take the blame here because the garment was wrongly labelled. Once the cleaner followed the inappropriate care label information the result was inevitable.
Rectification: a skilled dressmaker might be able to re-make the belt with a new interlining but there is nothing the cleaner can do.
Seam embossing spoils the appearance
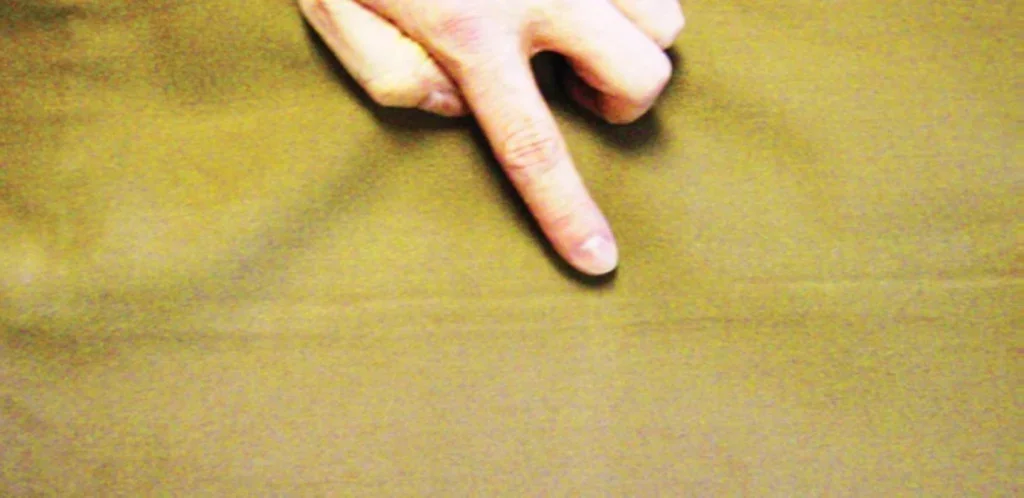
Fault: this ladies’ coat was well-made, and it cleaned perfectly. However, despite a relatively gentle press, it finished up with unsightly darker lines from embossing of the inner seams.
Technical cause: if this coat was pressed carefully by an experienced presser, then the most likely cause is hardening and compaction of the press clothing, probably as the result of slight wetness in the steam from the boiler. Once the press cladding gets wet and compressed and is then dried, it cannot provide the resilience needed to accommodate multiple layers of cloth, and marking of the type seen here is the consequence.
Responsibility: the blame here lies with the cleaner, because maintaining press resilience is regarded as an essential part of the cleaner’s craft.
Rectification: on this particular fabric, little improvement could be obtained, even after re-cleaning.
Collar grime not removed
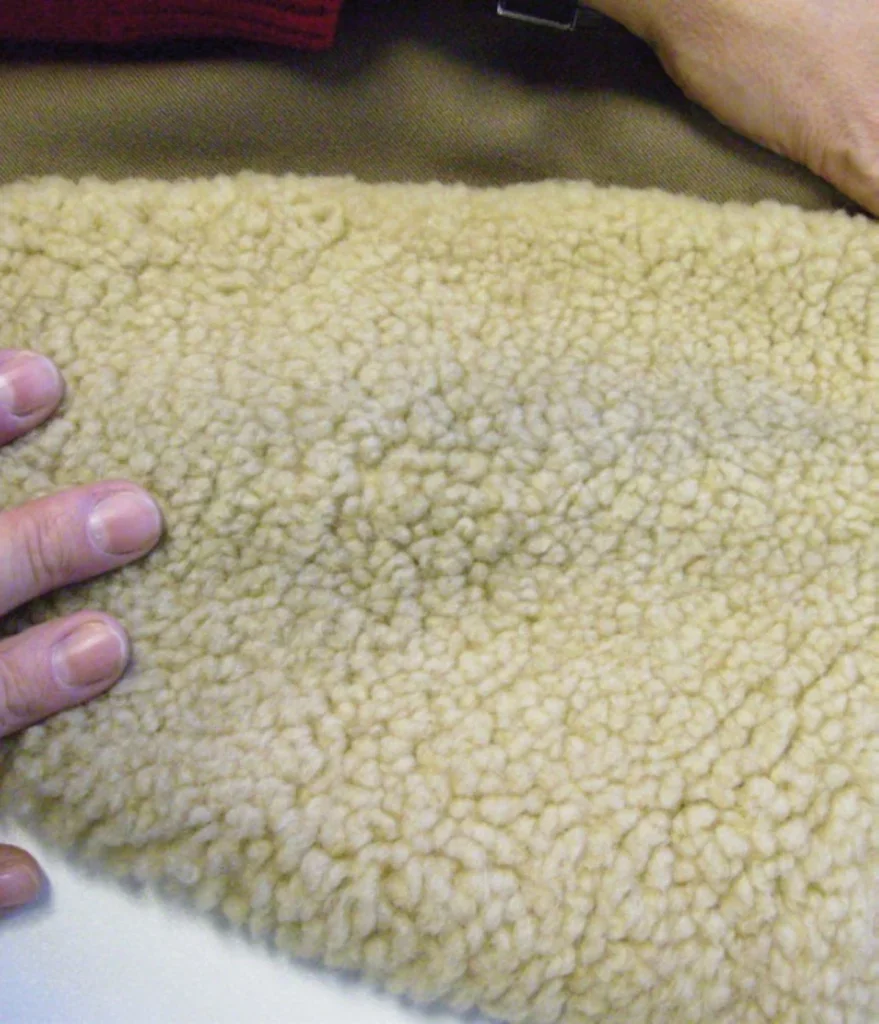
Fault: after cleaning, the owner was delighted with all parts of this natural fleece lined coat, except at the collar fold, where dark lines of ingrained soiling remained. The care label was P in a circle with no bar beneath.
Technical cause: deep seated ingrained soiling can be very difficult to remove from animal hair fibres, and on this coat, it had probably penetrated beneath the scalar layer, making it unlikely that it could be completely removed in drycleaning. In this case, to ensure the best possible result on the sheepskin fleece, the soiled areas should have been carefully prebrushed with a neat pre-brush detergent and immediately placed in the machine and cleaned using a thorough two-bath leather cleaning process, ideally in perchloroethylene. Dilution of the pre-treatment detergent with water raises the risk of felting and matting and should be avoided. The cleaner usually has only one chance to get this right because anything not removed first time may have become more firmly ingrained following cleaning.
Responsibility: stains and soiling are normally considered to be the responsibility of the customer and failure to remove either is unlikely to result in a successful claim. While it is highly likely that pre-brushing would have produced a better result, cleaners should always bear in mind that if kit pre-spotting chemicals or general pre-spotting reagents cause localized colour loss or damage, it is the responsibility of the cleaner.
Rectification: while pre- brushing with a general pre-spotting reagent might produce some improvement, this is thought to be unlikely in this instance.
Indelible handprint spoils the lining
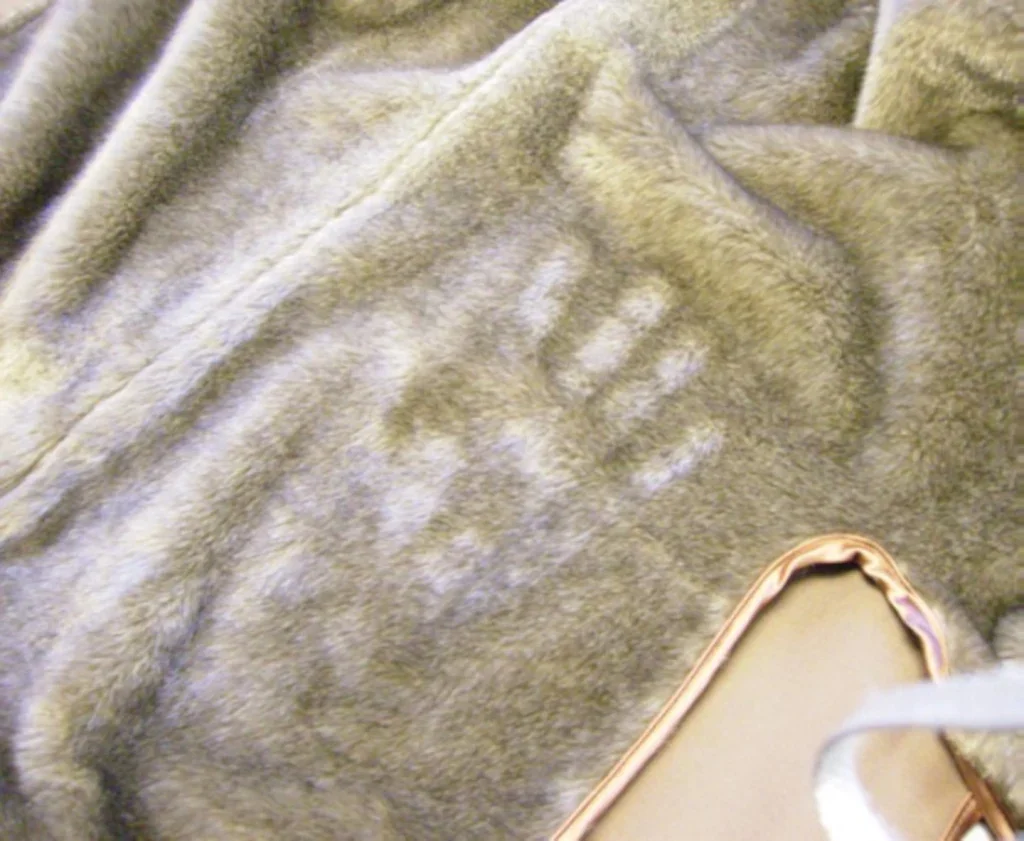
Fault: this fur lined coat came out of the drycleaning machine, in a very good, cleaned condition. However, the cleaner unwisely decided to steam finish it and immediately left a permanent handprint in the faux fur.
Technical cause: the fur lining to this jacket was identified on the material content label as a mixture of acrylic and modacrylic. The cleaner had lowered the thermostat setting for the outlet air temperature during tumble drying to comply with the precautionary bar beneath the P in a circle symbol on the label, so no damage occurred in the machine. However, when the cleaner decided to steam the coat, its fate was sealed, and serious damage was almost inevitable. Steaming the coat on the press softened both the acrylic and modacrylic fibres, so that as soon as the presser’s hand touched the fabric it flattened the softened fur permanently, with the result seen here.
Both acrylic and modacrylic fibres are thermoplastic and deform very easily under the influence of steam. This is particularly the case with modacrylic fibre. While acrylic knitwear can be steam finished (with great care – avoid moving or touching the fabric until it has been fully cooled with the vacuum), to prevent the very high risk of pile distortion acrylic pile fabrics (e.g. Dralon) and acrylic/modacrylic faux furs should not be steam finished. Acrylic pile fabrics should be carefully checked during reception for any signs of pile distortion (such as wear creasing in cushion covers), because any attempt at finishing to remove this could result in a major claim.
Responsibility: both the fibre content label and the care label in this garment were correct, so the blame lies with the cleaner.
Rectification: unfortunately, none is possible, but depending on the severity of the damage some improvement may be possible by bottom steaming. Unfortunately, this could also increase the severity and the extent of the damage.