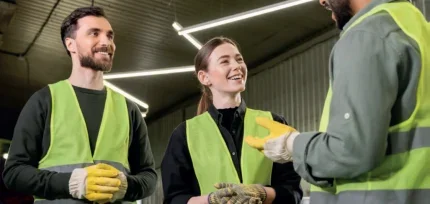
In the 1970s, sharp independent launderers worldwide recognised the latent demand from the pharmaceutical and electronics sectors for garments which were essentially free from particles and loose fibres or lint. A few trailblazers led the way and cleanroom garments rapidly became established as a premium rental product. Many tried to leap onto the bandwagon, but most quickly realised that to succeed, they needed to back up their product with in-house testing and advanced quality assurance. Those with technical skills and persistence succeeded in entering the markets and delivered a reliable product at an attractive, commercially viable price.
Delivering workwear against specific performance guarantees has now developed into several sectors. We take an overview of how this has been achieved and what is needed for success.
Liquid repellent garments
Some workers require garments which are liquid repellent, but not necessarily waterproof. If they go outdoors only occasionally, a showerproof but breathable fabric might be a more desirable option for adequate protection and long-term comfort. In stark contrast, an operative at risk of encountering an acid splash will require a garment which is effectively impenetrable to liquids. It must remain so after multiple wear and cleansings, so there is a duty on the rental operator to ensure this. However, it might not be realistic to rely solely for protection on any garment which has been worn and washed repeatedly, without some form of primary protection for areas of the body which are most at risk of contamination. This is usually achieved by the addition of a waterproof apron to cover the operative’s frontal area, with gauntlets to protect the wrists and forearm and a visor and helmet for the face.
Maintenance of liquid repellent garments should reflect the need to maintain the repellence for the next wearing. This might involve specialist wash chemistry, designed to not damage the repellent component or it could call for re-treatment with repellent every so many washes. This should be achievable using individual bar codes for each garment in the contract, to enable garments due for re-treatment to be identified by scanning during sorting and treated appropriately. If the repellence has been achieved using a wash-in process, then this might need to be repeated every single time the garment is processed, depending on the severity of the risk. These details should form an important part of the rental contract.
The rental customer will require some form of assurance that the cleansed garments are fit for service as regards absorption prevention. There are recognised methods for this, ranging from simple droplet test up to a laboratory measurement of hydrostatic head resistance using the universally trusted ISO method. The droplet test can be carried out daily, in-house, on each batch of treated garments. It involves placing one droplet of water on one or more treated garments from the batch and measuring the time taken for the droplet to become absorbed. A useful refinement for this test is to use the hazardous liquid at the customer’s premises, provided the safety conditions for this can be accommodated at the rental laundry and a specific acceptable absorption time agreed. The laboratory test method can then be applied at less frequent intervals as a double check that the systems are working satisfactorily.
High-vis garments
Many hi-vis garments achieve their superb reflectance using tiny aluminium discs embedded in a flexible plastic carrier layer. Even when new, the plastic layer is not totally impervious, so it is essential that the wash process does not involve anything which can attack aluminium. This rules out the use of any alkali (such as sodium hydroxide, sodium metasilicate or calcium carbonate) and explains why most standard commercial wash processes cause such rapid degradation of hi-vis fabrics. The solution is to formulate detergents for hivis using neutral ingredients, which works fine for dust and light grime. Removal of skin oils, from neck and wrist, requires a suitable emulsifier designed to work at low temperature with the correct HLB (hydrophilic lipophilic balance) value, or avoid reflective materials made from aluminium. Of far greater importance for hi-vis garments carrying mineral oil or grease contamination is to include emulsifiers able to solubilise these, if wearers have been working on rail and train maintenance for example.
The effectiveness of a hi-vis fabric after repeated wearing and cleansing can be measured using a specialist reflectometer. The meter is placed on the fabric and a light (made up of a standard mix of wavelengths) is shone from an angle. The percentage of the light reflected from the fabric surface is then measured using a photocell and this reading is recorded as the effective reflectance of the material. It is thus possible for the rental customer to specify the minimum reflectance acceptable, below which the garment must be rejected (and usually scrapped). The rental operator might be asked to monitor sample reflectance from each batch using an in-house meter. Or the rental supplier might agree with the customer the maximum number of wears which a garment can be allowed before it is scrapped. This would then be monitored using a bar code or similar system, with scanning during sorting.
Garments with low surface resistivity
Unwanted electric discharge across the surface of an operator’s garment can play havoc in the micro-electronic, paint spraying and even pharmaceutical sectors. A wide range of fabrics can accumulate a static charge and pose different risks to product quality, so it is necessary to select the fibre mix for the garment carefully and implement the appropriate control to ensure neutral electrical activity across the surface.
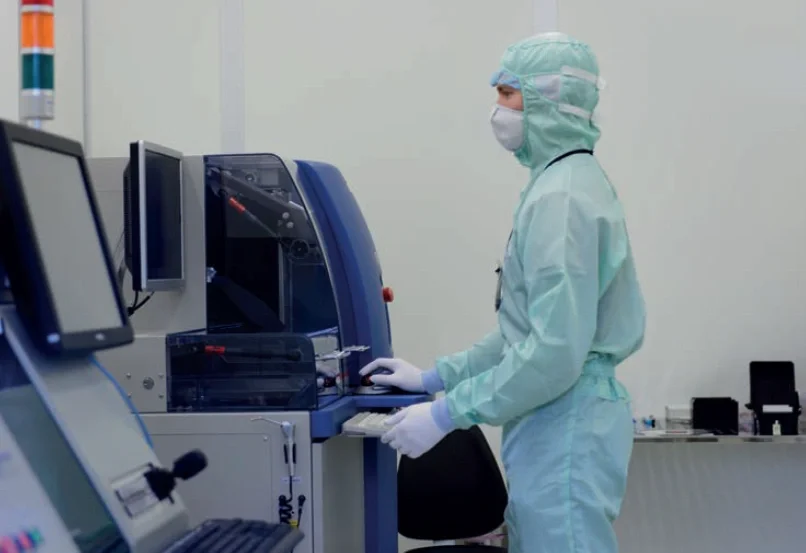
Assembling a roll of wool fabric after finishing and drying often builds a static charge running into thousands of volts, despite the high moisture regain of wool fibres. One cannot rely on the increasing pick-up of moisture from the environment to discharge this satisfactorily. In contrast, the inclusion of the cotton in a polycotton blend effectively reduces the risk of explosion in plants processing hydrogen, because the cotton does regain moisture and the risk of a spark occurring is very low.
The dissipation of a static charge on workwear can be achieved by creating a conductive finish on the cloth surface. This might be capable of withstanding multiple wear and cleansing (in which case monitoring the number of previous washes in sorting by scanning a bar code might be appropriate). Alternatively, the finish might need to be re-applied after every cleansing, making for less expensive garments, but higher processing costs.
Most success has been achieved by incorporating a grid of conducting metallic or carbon fibres in the weave of the fabric, which is a very robust way of ensuring total and uniform coverage of the protection. The grid in the weave is often very visible, aiding quality assurance.
‘Cleanroom’ garments with low fibre and particle counts
Again, it is the pharmaceutical and microelectronics and paint spraying sectors who led the way with demands for fabrics and garments which could be reliably delivered to users in a condition which was free from particles and fibres, even down to 10μ (ten micron) in size. Some sectors relied on disposable fabrics initially, but as cloth suppliers developed continuous filament yarns and fabrics able to withstand upwards of 50 wearing and cleansings, and launderers developed sealed cleanrooms, thing changed.
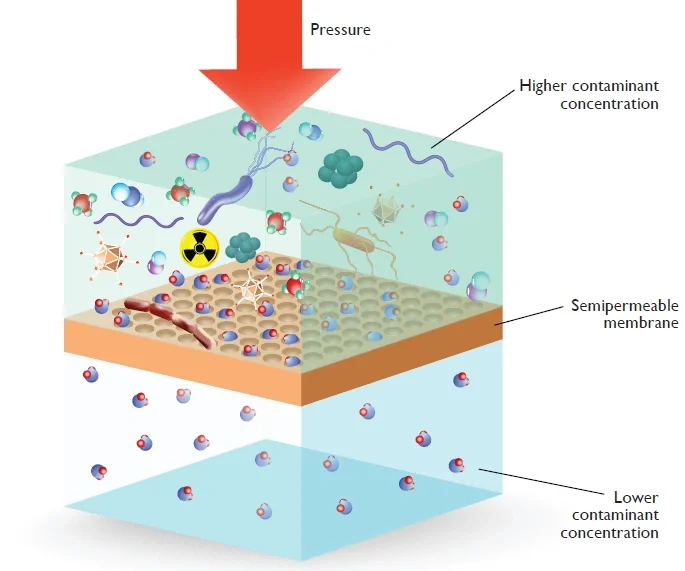
Cleanrooms were constructed and supplied with hepa-filtered air (which was effectively particle-free) and water purified by micro-filtration. By keeping the cleanroom at a slightly positive pressure, sealed and with airlock entry, rental operators achieved basically particle- and fibre-free environments. The fitting of hepa-filters in the cleanroom ceiling enabled downward laminar flow of incoming air, so no turbulence to disturb anything. The extension of inlet water treatment to improve disinfection by UV radiation reduced the risk of bacterial penetration from mains water, which was of particular benefit to pharmaceutical customers. Rental operatives were clad in cleanroom garments themselves (from head to toe, greatly reducing the risk of particle and fibre pick-up from hair, skin and clothing.
Quality assurance can by achieved using a Coulter counter to monitor particle contamination on a continuous basis. Fibre counts can be estimated by the latest counters, but the older method of drawing a known volume of air through a fine graticule and counting the number of fibres in a 25 x 25mm square is still very viable. These techniques enabled the rental operator to meet customer requirements for assured quality with numerical results always available. It also meant that the need for external laboratory measurements was greatly reduced, being used for checking the in-house methods rather than needing to be used for every batch of garments.
Antibacterial garments
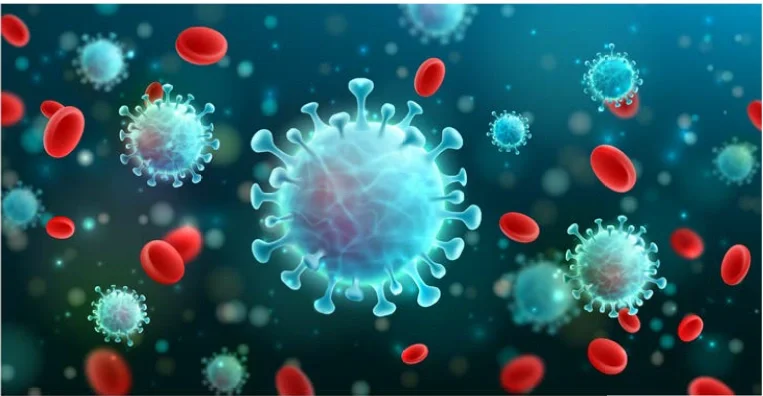
Garments for wearers in the pharmaceutical industry are frequently required to be not only free from bacteria but also treated with an antibacterial finish, so that they are resistant to picking up viable bacterial contamination. The historically acceptable method of disinfecting healthcare garments was via implied thermal disinfection, involving a wash process that gave at least 3 minutes (plus mixing time) immersion in water at or above 71C. This has now given way to chemical disinfection, usually in the final rinse of a healthcare wash process. However, achieving antibacterial properties on the garment fabric requires slightly more than chemical disinfection, and modern processes that leave a suitable bacteria resistant finish on the fabric surface involve a substantive residue which bonds to the fibres and yarns. Until recently these finishes would probably have involved a quaternary ammonium compound (a ‘quat’), but there are better, more robust alternatives now available. Again, for the most demanding duties, for which antibacterial performance must be assured, it may be necessary to monitor the number of wear and cleansing cycles and to either re-treat or scrap the garment after a specific number of cycles.
Conclusion
The specialist market for the types of workwear described is a typical example of the premium product which the rental market is capable of providing. It calls for modern quality assurance using some of the newest techniques now available to the rental operator. This makes a refreshing change from customers concentrating purely on the price of the product, to one which takes into account the technical quality of the offering and the technical assurance which goes with this.