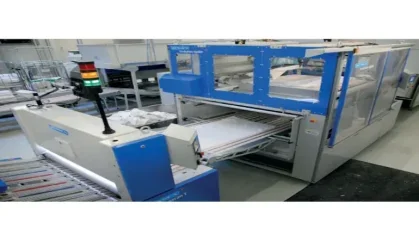
The textile care sector in Scandinavian states is slowly growing thanks to the lifting of the majority of restrictions associated with the pandemic in the region and generally high seasonal demand for laundry and drycleaning services – although problems still exist.
Despite the fact that most of analysts expect a further growth of regional economics this year, they agree that such growth will be significantly lower those expected at the beginning of the current year, not exceeding 1.5%. The main reason for this is the ongoing energy crisis in Europe and the existing fears of the complete suspension of the supplies of gas from Russia.
That puts additional pressure on the textile care sector in the Scandinavian states. The analysts’ fears are confirmed by representatives of the industry and some major players.
Daniel Kärrholt, director of the Swedish Textile Service Association says he does not see any visible growth of the industry this year. “Most segments of the industry have not really recovered from the pandemic. Many meetings are still digital and the physical encounter when wearing business attire has not really returned to the same level. Right now, there is a seasonal high due to graduation and wedding.
“For those members that combine healgthcare with hospitality customers the latter sector has provided a much needed surge in demand. What we need is for conferences and the business travels to pick up. We will see how it develops in the autumn. An increased spread of infection would be very troublesome. We are seeing a growth in household laundry thanks to the RUT tax deduction on household services – since 1 January 2021, the RUT deduction applies to laundries. This means that the cost of household laundry is reduced by 25%. This is applied to all laundry that could normally be washed at home, including minor repairs and transport.”
The existing challenges are confirmed by most of leading industry’s players although the majority plan to continue their expansion in the regional market this year.
Christoph Kampmann, Alliance Laundry Systems’ director of distribution Europe says that ALS has installed barrier washer-extractors in various hospitals throughout Scandinavia, both in refurbished and new locations. “The barrier washer solution was also installed in several nursing homes and fire fighter departments throughout Norway. More specifically, our customer Nortec in Denmark converted many obsolete laundry installations into some of the most modem energy-efficient laundries throughout the country.”
According to Kampmann, the Scandinavian market for laundry is growing after Covid since tourism is coming back, resulting in an increased occupancy rate in hotel facilities.
“We also notice the increased demand for connectivity in the laundry facility. ALS focuses on this already for a few years, resulting in the availability of touch controlled machines and data management platforms allowing laundry managers to access data of their laundry operations remotely and take business decisions consequently. This increases the efficiency of the whole laundry process even further. Scandinavia is also the region in Europe which is typically most sensitive for ‘green’ solutions. Also here, Alliance offers several products in order to answer this demand, such as heat-pump dryers as well as washers and dryers with a reduced kW-rating."
As for challenges, finding technical people such as service reps, according to Kampmann, currently remains one of the major tests the company faces in the Scandinavian market.
In the meantime, despite the ever-growing energy prices and some existing geopolitical threats to the region, other global majors have no plans to slow down the pace of their Scandinavian expansion.
For example, representatives of Kannegiesser have said that the company has made some serious achievements in the Nordic market in recent years. Felix Goehner, an official spokesman at Kannegiesser, comments: "We have multiple projects in development that are still in the planning phase. Last year we installed a new washing and garment solution for highest demand in productivity and resource savings at De Forenede Dampvaskerier A/S in Aalborg. The garment system includes the tunnel finisher XMT and the folding robot FA-X. The washing system consists of the batch washer PowerTrans Vario, the centrifuge PowerSpin and 6 PowerDry batch dryers."
According to Goehner, in general, the Nordic laundry and textile market is highly competitive and fairly saturated. "However, our sales show that our innovative and customised solutions continue to be well received. A major focus of ours, and certainly one of our strengths, is to provide sustainable solutions through intelligent resource management systems that save energy and water. Due to constantly rising energy costs, new EU directives to conserve resources and the clearly visible effects of global climate change, sustainability is increasingly becoming the focus. For us, sustainability is an elementary component and more than just a trend. Textile service providers and their customers are more and more focusing on sustainability. Kannegiesser therefore provides advisory support to their customers.
"By helping our customers become more sustainable, we too can play our part in reducing the resource demands of the textile service industry. This is made possible by using new technologies in our research and development," says CEO Tina Kannegiesser. In the washing area, the high-performance washing line PowerTrans Vario sets new standards for wash quality, hygiene, water and energy consumption. The water-extraction technology of the PowerPress and PowerSpin provides low residual moistures permitting high savings in the subsequent evaporation process. With the PowerDry batch dryer, the Eco2Power process control ensures that the energy remains in the system and does not have to be recovered via heat exchangers. In the finishing process, Kannegiesser is a pioneer for low-temperature drying during the process of ironing, finishing and full drying – with impressive results for both maintaining textile value and energy consumption. Ultimately, the energy contained in the ironing and garment finisher exhaust air is used to heat fresh water for the washing process – the circle is completed.”
At the same time, Jensen Group sales director for the Nordic area Lars Borg, says the company sees some new trends in the Nordic textile care market. “The concerns of customers and operators during the pandemic have resulted in a growing demand for more hygiene: Better health and safety to protect the workers in the laundry as well as improved hygiene standards in the provided linen services. Automation and technology helps laundries to reach these goals and move the operation’s services and working place to a next level. Laundries in Scandinavia quickly responded to this new approach, and heavily invested in new automation solutions and robotics.
“The handling and sorting of healthcare garments has been a nearly hands-free operation for many years. The Swedish laundry Textilia in Boden trusts Jensen technology because of its high sorting accuracy. Their new system is being handed over. Work is in progress with the same technology at Segersby Laundry/ Sweden and Vraa Laundry in Denmark.”
Borg explains that the robotisation of Scandinavian laundries is accelerating. The Oslo branch of NorTekstil awaits an entirely new soil sort system for all linen. Automation is key to NorTekstil that has already invested in an automated stack storage and pack-out system for clean linen. Also the folding and sorting of terry towels can be done in an automated process, combining a robot and a towel folder. The robot takes care of the automatic separation, feeding and placing of towels into the towel folder. JD Tvätten in Sweden is extremely satisfied with the production figures and confirms that 'they would not want to live without it'."
Robotics are no longer exclusive to large groups. Small to mid-sized laundries have recognized the opportunities by automating repetitive and heavy manual work. Robotic sorting and Futurail sorting installations – be it as stand-alone individual solutions, be it in a combined system – for the soil and clean side are increasingly popular for laundries of all sizes. One of the smaller laundries in Norway has recently upgraded its plant to become a full RFID laundry with automated sorting. Its modular system can be engineered to fit all requirements of laundries with large volumes as well as for laundries that are planning to grow their volumes.
In the meantime, the attention of many industry players is turning to development of new industry products. Thomas Zeck, commercial director of Kreussler Textile Care, comments: “We have been doing field tests in several laundries with a new product that is an environmentally friendly alternative to chlorine bleach, and we are extremely happy with the results. The bleach activator enables fast, fibre-deep oxygen bleaching at low temperatures, increasing whiteness as well as the life cycle of the treated textiles. The new bleach activator ticks several green boxes at once. Its high concentration and efficiency help to save resources: Even minimal amounts intensify the bleaching activity of oxygen bleaches that much that rewashing is reduced to a minimum; thanks to the possibility of washing at low temperatures, energy costs can be reduced even further. And as no dichlorination is necessary, additional costs for water treatment are saved as well.
"On top of that, the environment and the people working in the laundry profit from it as bleaching with chlorine leads to the building of noxious substances that are difficult to degrade and harmful to the environment and health. The prolonged lifetime of the textiles is another sustainability factor, as not only does chlorine damage textile fibres pretty well by itself, but the necessary anti-chlorination offers two additional potential disasters: if not enough active oxygen is used to neutralize the chlorine, residues of chlorine bleach remain in the fabric, leading to extreme textile damage to the laundry and the flat work ironers wrapping during drying. If, on the other hand, too much active oxygen is used, protein stains in the pre-wash can irreversibly 'burn in' due to active oxygen residues when the water is recovered and used again. And, of course, longer-lasting textiles and machinery mean higher cost efficiency, spelling good hard cash for their owners. Adding the savings for water treatment and due to lower temperatures, the new product will be a great choice for any laundry that wants to make their bleaching process more sustainable.”
According to Zeck, the company sees a very positive growth of smaller and middle-sized laundries. For them as well as for larger industrial laundries, quality is becoming more and more important, while price is not necessarily the decisive factor anymore. In general, the demands in terms of both quality and sustainability increase.
Zeck continues: “In fact, one of the most important Kreussler innovations is developing strongly in the Nordic market: we see lots of classic dry cleaners changing to the wetcleaning technology we invented in 1991. It provides the ultimate level of sustainability in caring for even the most precious garments, as Lanadol wetcleaning uses water as a solvent, combined with the biodegradable special cleaning agents of the Lanadol product family, to treat fibres with extreme gentleness. It is the only wet cleaning enabling to skip the pre-brushing step for up to 95% of textiles, allowing a return of the cleaned garments in less than an hour. The remaining few extremely sensitive textiles can be cleaned as thoroughly with a supreme level of care and fibre protection, even offering a powerful, but gentle hygiene rinser for delicate garments that can not be treated with conventional disinfection procedures, for example, in nursing homes.
“Of course, there are challenges as well, but they are not restricted to the Nordic market nor to our company: the whole world is challenged currently. Both the Covid pandemic and now the war in Ukraine affect all markets. We have an unprecedented crisis in the commodity situation: many important raw materials have become drastically more expensive; for some we have seen enormous price increases of 40%–80%.
“This is accompanied by an increasing shortage of available materials. The same trend can be seen in the areas of packaging, logistics and services. In addition, there are supply bottlenecks for example for pallets, the prices of which have more than doubled compared to the previous year. Due to the political situation, we face enforced challenges regarding energy supply: there is no security regarding availability and required infrastructural conditions. Add to that the climate crisis means using less energy in general, and we have a challenging mix of a multitude of unexpected and unpredictable factors which will keep our market on its toes for a considerable amount of time.”