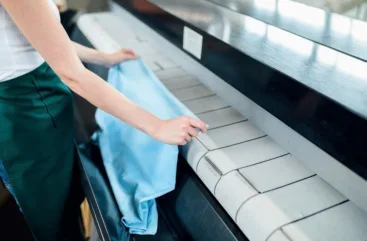
These recommendations are designed to identify what tips the the laundry engineer can give to really help the laundry manager. This is one of the keys to success with healthcare textiles and has been fundamental to the astonishing increases in healthcare laundering productivity and cost management which have taken place over the past few years.
Ironing
Variations in ironer efficiency is understood to be behind some of the largest variations in laundry performance across the healthcare sector. The main points to watch were described in the Jul/ Aug 2022 issue of LCN. They indicated how to ensure and monitor uniform bed temperatures for both steam-heated and thermal oil ironers, as well as the importance of achieving and maintaining correct vacuum to the rolls.
Thin bed, steam heated ironers have high condensate rates flowing through the thin bed. The internal plates need to be kept free of any build-up and the steam traps must be sized to clear condensate at the rate at which it is formed and checked regularly. Float and inverted bucket traps are probably the best choice for these, with adequate and correctly set steam lock release systems.
Calender wax can blind the clothing, especially on the front roll, which means the method and frequency of waxing is critical. Using a proper waxing cloth at the correct intervals, with an appropriate quantity of fresh wax calls for good training and supervision.
Maximising bed coverage by edge to edge feeding and use of every lane is fundamental to productivity, but this is frequently not achieved. The laydown from the feeder should be set carefully and the workflow to each ironer controlled so that the usage of the heating area is maximised. This might require some careful work to achieve but it is worth doing this properly. It is the key to maximising throughput.
All ironers are designed to operate with controlled roll-to-roll stretch, to maintain good contact between textile and the bed. Where the design allows this to be set by the engineer, it is important that this is done correctly. The precise figure for each model is given in the manufacturer’s manual. This is so important that many makers supply metal tapes to check the circumference, especially where the finished diameter of each roll varies.
Some ironer beds can and distort over time. This can be detected by checking the point at which each roll closes on the textile at the in-running nip, which a good laundry engineer will do regularly. If wide variations are found, roll to roll, then discussion with the manufacturer is needed.
Safeguarding for better efficiency
Crunch time has come and much of the world is now having to deal with potentially catastrophic increases in energy prices. Now is not the time to put our heads in the sand or to limit your reaction to trying to negotiate large price increases with customers who are understandably grumpy and uncooperative. Support from national governments is unlikely to mitigate the problem significantly or longterm.
However, there is much that can be done within every textile care operation serving the textile rental and contract laundering market. The essential immediate steps require team effort and careful thought, but they need not demand substantial investment (other than in man hours) and they have been proven to produce substantial reductions in energy demand, with corresponding financial savings, which will be particularly useful in the current climate. Don’t lose hope until you have read and acted upon our review of recommendations.
Stahl now has a compact roll ironer, which can be seen at Texcare 24, which has been added to its range of ironers. The heated roll ironer is easy to operate, requires little space and is particularly suitable for small businesses. The manufacturer, which is actually known for its powerful large ironers, is thus closing the gap in its range of compact appliances.
From Tolon, visitors can see Upgraded ironers now featuring 350 mm and 600 mm diameters for superior ironing performance, says the company.
Valmet is the mainstay for maintenance items for feeding and folding apparatus and ironers. It produces needled felts for the feed belts and the covering of the rolls of all types of flatwork ironers (heated roll and heated chest).
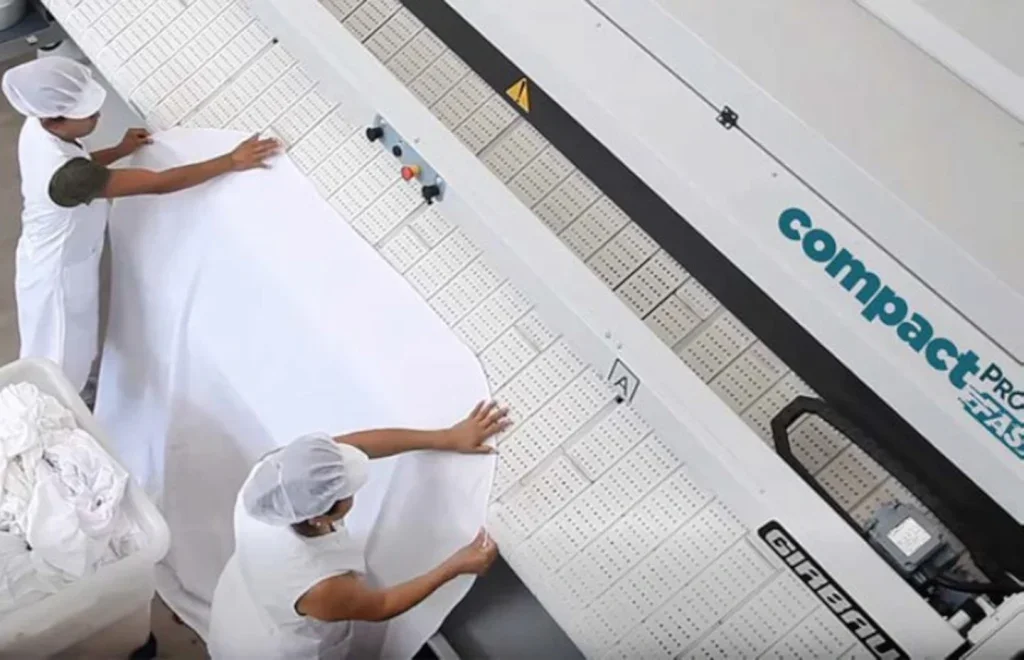
Domus wall flatwork ironers with TOUCH II technology and Eco-Energy CM-2050, 2650, 3350 are calender machines for laundries with significant working volumes
These machiones have a long list of strengths and advantages that make it a profitable investment for any business. It has been designed to achieve high levels of productivity with maximum energy efficiency, optimising laundry in terms of time and consumption. It is an industrial ironing machine with which your laundry system will leap into the future. Turning this investment into necessary, safe, and profitable in equal parts,” says Domus.
Meanwhile, Lapauw poses the question: “Did you know that the flexible chest technology is in fact a Lapauw development? And the ‘steamless laundry’ concept would not even exist if it wasn’t for gas heated ironers, a technology that saw the light in the Lapauw factory. Ever since the very first ironer, in 1950 (with flexible chest), Lapauw has been on the vanguard of laundry technology. Lapauw always adopted an ‘out of the box approach to the specific challenges that come with laundry machinery.”
Lapauw adds that most important of all, owners of the more than 8000 machines sold in over 40 countries know the Lapauw machines as highly efficient, long lived machines that assure the lowest operational cost.
Girbau’s PC Series ironers and Compact Pro system, pictured above, are designed to ensure top-quality results while optimising operational efficiency.
Girbau explains that its PC Series ironers are built for maximum productivity, with speeds up to 50 m/min for the PC120 model. They ensure superior ironing quality thanks to their polished bed design and advanced electronics. Each roll has an independent motor, improving heat transfer and ironing pressure for greater efficiency.
Durability is a hallmark of the PC Series, featuring Rigid Technology for resistance against mechanical and thermal stresses. These machines are easy to maintain, minimizing downtime and reducing wear on consumables. More than just a productivity booster, the PC Series delivers a flawless finish that enhances the appearance and longevity of textiles., says Girbau.
Girbau’s Compact Pro system is a spacesaving powerhouse, integrating feeding, drying, ironing, folding, and stacking into a 20m² footprint. Ideal for tight spaces, its modular design allows for easy installation. The Smart Touch Strap technology maximizes fabric contact with the roller, while Autospeed maintains consistent ironing temperature. The Smart Heat feature cuts energy consumption by up to 30%, making it both efficient and eco-friendly.
Girbau’s PC Series and Compact Pro offer the perfect combination of productivity, quality, and efficiency, making them essential for any industrial laundry seeking top-tier performance and results, says the company.