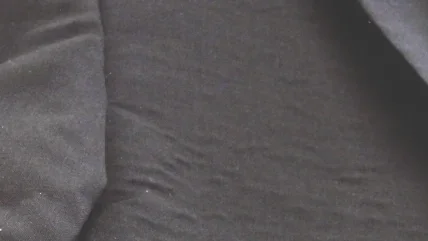
Fusible interlinings were first used in garment manufacture around 1956 to enhance the stability, drape and handle of items such as jackets and coats. Today they are widely used throughout garment manufacture and over the past 68 years they have been responsible for some of the most common and frustrating recurring finishing problems. There are many interlining types and it is critical that the manufacturer selects a good quality product appropriate for the garment type and follows the precice parameters that must be observed when securing interlinings to the shell fabric. It is also important that new product lines are tested against BS / ISO 3175 to confirm the long term cleaning performance of the interlining / garment combination.
At the counter
In the first instance it is essential that garments are carefully checked at reception, to establish as far as possible, that there are no pre-existing interlining faults. Counter staff need to be vigillant and always on the look out for for any sign of bubbling or rippling in the areas of items where fusible interlinings are located such as the the front facings, lapel / collar areas and shoulder areas of jackets. Faults found during reception may be the result of the age of the item in conjunction with normal wear and tear or even mishandling by the customer and should of course be brought to their attention together with an informed discussion of possible outcomes and, if thought necessary, the use of ‘owners risk’
Low volume manufacturer, designer and tailor made suits can be prone to interlining problems. In the case of tailor made items in particular, fusible interlinings may be introduced by means of hand ironing which by it’s very nature lacks the precision of the automated processes used in the production of mass produced items.
Correction techniques
The rippled effect which is perhaps the most common fault develops when differential shrinkage takes place between the interlining and the outer fabric, drawing the outer fabric into the well known rippled effect. The fault may be due to incompatible components used in manufacture, but liberal and random use of water based pre-spotting products at interlining locations or drycleaning garments that may be damp or wet can also be the cause of the problem and is, without question, the responsibility of the cleaner. Bubbling occurs when the adhesive bond between the interlining and the outer fabric breaks down in one area leaving the outer fabric locally unsupported.
If the faults are not severe they can often be rectified or at least to some extent corrected. In the case of rippling, steam the affected area and while the fabric is very hot, stretch the affected area at right angles to the ripples – sometimes you may need help with this. After stretching out the ripples hold the fabric under tension while applying plenty of vacuum. It is important to cool the fabric until it is completely cold. Then press and vacuum with the head locked or iron firmly while applying vacuum. For bubbling try applying a light mist of a good quality hair spray to the affected area before pressing. This will slightly stiffen the fabric and often enables the finisher to produce a satisfactory result.
Finally, cleaners should bear in mind that interlining faults can be the result of mishandling by the customer; good examples of this being tumble drying of damp or wet items following exposure to wet weather.