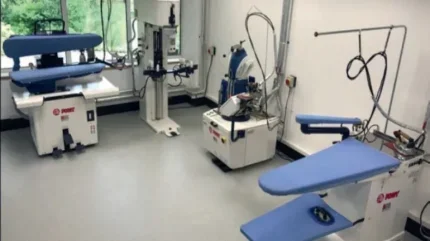
In this first article I will be looking at scissor presses, however steam pressure and vacuum efficiency are also applicable to ironing tables. The following are standard industry tests and checks that any cleaner can use to establish the condition and performance of your equipment. They will enable you to quickly identify faults that may be seriously affecting quality and production rates.
Steam
The correct steam pressure for finishing equipment is 55 – 70psi. (3.7 – 4.8 bar) however steam response begins to drop off approaching 55psi and a good average working pressure to aim for would be 65psi. (4.4bar). In addition, as the steam pressure falls towards 55psi the steam may become too wet for optimum finishing conditions.
Steam response: this refers to the time taken for steam to appear at the surface of the bottom buck/ironing table after pressing the steam pedal. Good steam response is vital in terms of quality and production rates.
On manual presses with steam supplied from a central boiler a response time of no less than 2 ½ seconds 789 should be expected. Automatic presses with their own boiler can be much slower with response times often above 6 seconds.
To check the locking pressure, vacuum and its distribution and the alignment of the bucks you will need a sheet of A4 printer paper.
Locking pressure: ideally this should be checked at the start of each working day. Place the paper across the narrow end of the buck and lock the head and adjust the locking pressure so that it is possible to withdraw the paper without risk of tearing it.
Alignment: carry out the same check at the wide end. If the bucks are correctly aligned the locking pressure should be the same at both ends, if it is not the alignment of the top buck needs to be corrected.
Vacuum efficiency: there are two checks – both can be used for ironing tables.
1. Using at least 5 seconds steam heat the bottom buck, then apply the vacuum and quickly run a hand over the whole surface of the buck. A good vacuum should completely cool the surface within 5 seconds. If bottom steam and vacuum are applied simultaneously a good vacuum will completely take away the steam.
2. Using the A4 paper, vacuum distribution can be checked by placing the paper at several points on the buck, apply vacuum and then drag the paper off the buck, this will reveal the vacuum strength at various points.
Some common equipment faults that can seriously reduce production rates.
- Head checks/dampers not working
- Press heads not locking reliably
- Hard, consolidated press clothing
- Rapid head closure on automatic presses. (this is dangerous and can also disrupt press lays)
Finally, the safety guard/system on automatic presses should be tested at the start of each working day. In September I will be looking at press/ironing table clothing and garment formers.