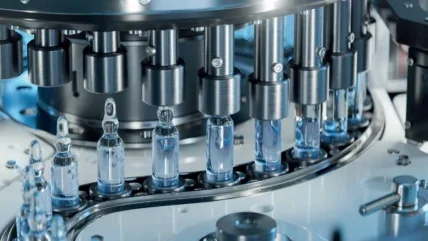
History of the cleanroom
Although it may be an exaggerated folk tale, there is a delightful story in the UK of how an astute and technically very competent launderer, sitting next to a micro-electronics engineer quite by chance on an aeroplane, first learned of the problems concerning particulate contamination in the high-tech workroom. He realised that here was on opportunity for the UK garment rental sector to meet an expanding need, sowing the seeds for the very successful, high volume cleanroom garment operations in the UK today. Others in the US and the Far East may have been way ahead of this, spearheading the major market which now serves the enormous, worldwide micro-electronics industry (and the equally large pharmaceuticals sector). This month we look at what is involved in meeting the demands of this market and the changing (and challenging) performance standards required.
Market requirements
The micro-electronics sector needs to fit a seemingly ever-increasing number of components onto a single chip, so the size of any particulate contamination is getting ever more critical. Anything which can bridge across these tiny adjacent circuits must be eliminated. The number of particles contaminating a worker’s garment can be linked directly to the number of failures in a batch of micro-electronic product, so there is a significant cost advantage in getting the cleanliness right. It follows that if the cleaned garment is effectively decontaminated to this degree, then the conditions in the laundry must be every bit as good as those in the microelectronics plant. It is hardly surprising that many launderers considered only briefly what was then a tiny new market and dismissed the idea of entering this as too difficult, unrealistic and not for them.
Manufacturers of ethical pharmaceuticals had for many years recognised the need for complete decontamination of their products, both as regards micro-organisms and particulates. They proved to be a ready and receptive market for the rental operators able to meet micro-electronic requirements, recognising the ‘every particle is a bus for a bug’ analogy. Equally receptive, if more slowly, were the automotive manufacturers implementing the latest car finishes, which are prone to the visible blemishes which appear around every stray particle on the painting production line. They also had stringent additional needs concerning electrical charge on the surface of the car sprayer’s workwear.
Workwear fabric
Textile technology is a mature science worldwide, so it was not surprising that fabric and garment makers were able to react swiftly with workwear fabrics and manufacturing techniques to meet the need here. Natural fibres were effectively ruled out because of their variability and tendency to shed particles readily. Polyester fibres could be produced to a much more consistent quality as regards diameter and resilience to folding and abrasion, both in manufacture and in use on workwear. Fibre diameters were first optimised to enable resistance to abrasion and flexing with minimum particle shedding. Yarn construction was then devised using continuous filament yarns, which reduced mechanical damage and the shedding of short fibre lengths (when compared with spun filament yarns). The other advantage of a synthetic fibre was the ability to control the chemical content, which might give potential control over properties such as conductivity and colouring or surface finish. Garment making required the minimum of sharp folds in the fabric (because of the increased risk of abrasion causing particle shedding on the knuckle of the fold), care with joint construction and general design to minimise risk of mechanical damage in use.
Construction of the cleanroom
The cleanroom is constructed of impermeable materials that do not shed particles in normal use, with impermeable joints. The room would normally have an airlock entry, so that it can be operated as a slight positive pressure, thus ensuring that any leakage is from inside to outside. Air entry is via the ceiling using hepa-filters to remove particles down to, say, 0.1μm (i.e. 1/10th of a micrometre or 1/10,000th of a mm). Advanced micro-filtration can now take out even finer particles. Cleanrooms are frequently designed to deliver filtered air in laminar flow downwards, to minimise disruption and encourage settlement of the few particles that might still be present, so a large percentage of the ceiling area is occupied by the outlets of multiple fans. This enables a high number of air changes to be achieved, whilst still maintaining laminar flow. Some cleanrooms are designed with turbulent flow downwards, where a more uniform particle concentration is needed (which reduces the risk of ‘dead spots’ where particles could accumulate unnoticed). The launderer does not need to mirror precisely the cleanroom conditions of every client, but it is important to be able to understand these needs in order to operate a cleanroom which can meet the full range of clients’ requirements.
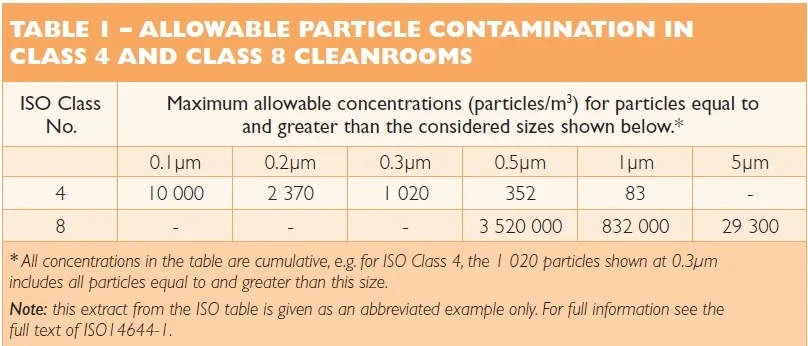
Mains water supplies vary widely as regards particulate and bacterial contamination, so these must be filtered out or destroyed. Micro-filters have been developed, with automatic periodic backflushing, backed up by very effective osmotic membranes which can filter almost down to the molecular level. Any bacteria which get through are then reduced using in-line UV treatment.
Barrier washing should be employed, using either washer-extractors or, conceivably, a tunnel washer, enabling soiled work to be loaded without contaminating the cleanroom atmosphere. The drain from the washer should be sealed with traps, to prevent any micro-organic or particulate entry from the exterior. Washer vents should be ducted outside the cleanroom with similar protection.
Cleaning the cleanroom itself is best done with a suitable vacuum cleaner, positioned outside the room and coupled through the wall to a hose on the inside.
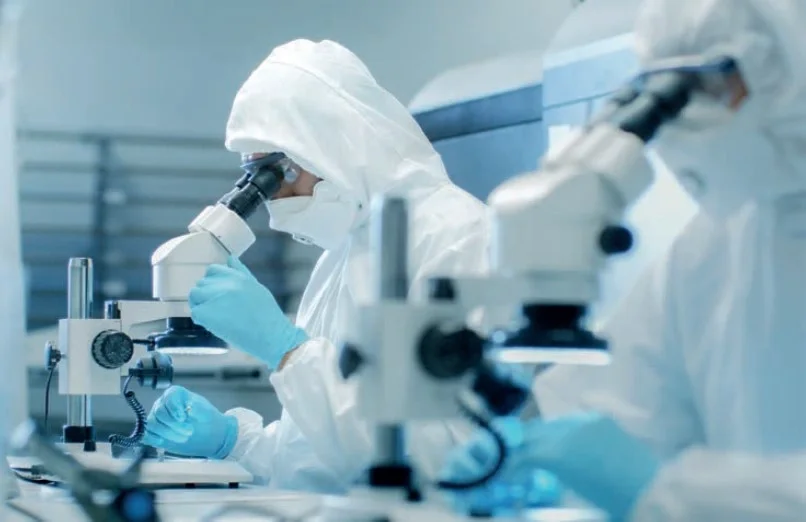
Any dryers or finishers should only draw in air through suitable hepa-filters and discharge to atmosphere outside.
Operative contamination
Operatives in the cleanroom can be expected to shed particles continuously from any exposed hair and skin, so personnel should be covered from head to toe in garments and protective coverings, designed to comply with the same standards as those to which the cleanroom is designed. They may be required to change into clean garments and coverings every time they enter or re-enter the cleanroom, in order to maintain the conditions demanded.
Decontamination standards
National standards were the norm in the early days, but as the markets grew and worldwide supply chains developed for every type of product, including microelectronic and pharmaceutical ones, rationalisation was required. Gradually the use in the USA and neighbouring areas of Federal Standard FS209(sections A to D), with particle concentrations in number per cubic foot gave way first to number per cubic metre in FS209-E1. Meanwhile in the UK, BS5295 was developed using SI units throughout, which is now obsolete. Then some impressive work by the International Standards Organisation led to ISO 14644- 12, which specifies the permitted number of particles of various sizes in nine levels of cleanroom quality, from Class 1 to Class 9. For example, the quality required for Class 4 and Class 8 cleanrooms are as shown in Table 1. General guidance to current international standards is available online3.
It is interesting to note that each ISO Class allows 10 times the number of particles than the previous one, in each size range. So, for example, Class 1 allows maximum 10 particles at or above 0.1μm, Class 2 allows 100, Class 3 1000 and so on.
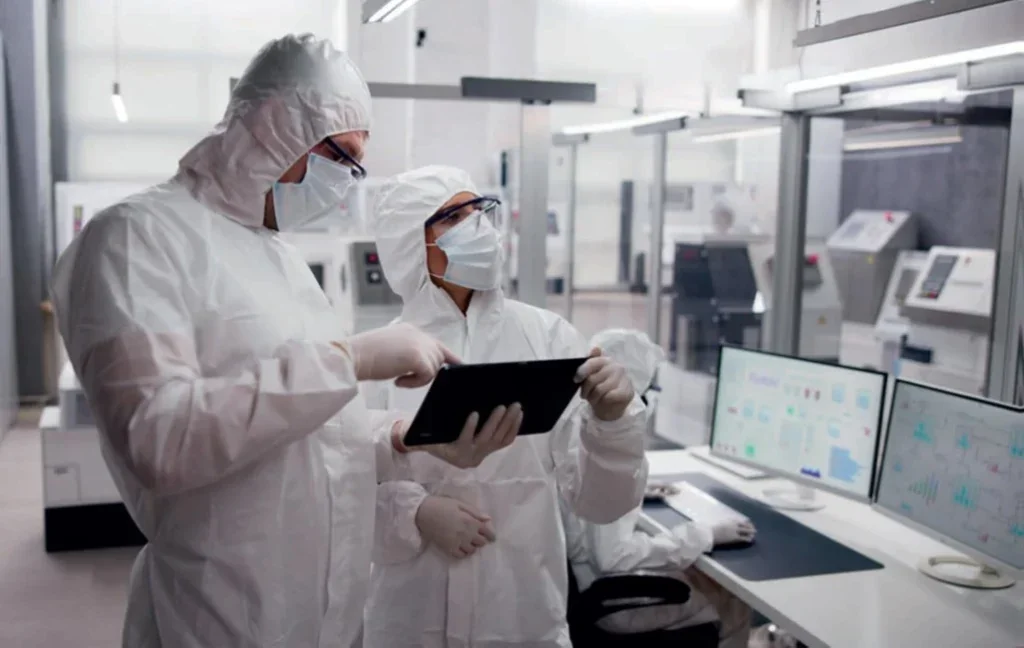
The ISO has now published four further sections on Cleanroom requirements: ISO14644-2 deals with Testing and Compliance; -3 covers Methods for Evaluating and Measuring; -4 describes Cleanroom Design and Construction and -5 covers Cleanroom Operations. The entire suite is essential reading for successful entry into this garment rental market.
Packaging
Correct packaging is vital for completing the cleanroom garment service. At present, packing each garment in a selfseal plastic wrapper is the universally preferred method, but this introduces the issue of a single use plastic, which could well be outlawed in the future, depending on recycling facilities and costs. As each wearer should be donning the garment in the clean entry area to the workroom, it s conceivable that wrapping multiple garments in a single wrapper might be achievable.
Conclusion
The rental market for cleanroom garments is an outstanding example of the sector identifying a commercial need and designing the fabric, the garments and the cleaning techniques required to meet the demand (and indeed to get ahead of the demand) with a product range which meets market needs consistently. It demonstrates how an outstanding level of quality assurance can be achieved without the need for rebuilding the traditional laundry. The concept of cleanroom processing in cleanrooms within the workroom is now well developed, and although it does call for significant investment in construction, equipment and training it is not beyond the reach of most established and competently managed laundries.
The development of this market has also involved considerable help and expertise from national and international standards bodies, working with industry technicians, to produce documented standards covering all of the technical aspects of this business, which is a credit to all involved.