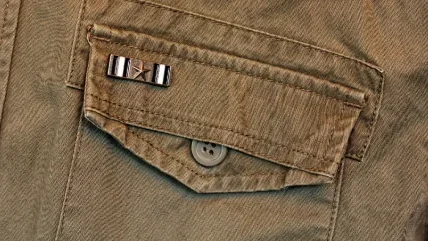
This month we continue the topics we raised in the May issue of LCN, with some case studies, highlighting traps for the unwary cleaner when handling items with trims that are unsuitable for cleaning (whatever the care label might promise to the contrary). The reluctance of a great many retailers, even chains with multiple high-volume outlets, to check the cleaning performance of the ranges they have for sale, is nothing short of scandalous. British and international standards organisations have made available, with considerable effort and cost, methods for correctly testing new garment ranges and it is disappointing and frequently infuriating when these are ignored by designers, buyers and retailers.
Responsibility
Bear in mind that, in the case of plastics and paint finishes, any mark-off onto other garments during cleaning is usually taken to be the responsibility of the cleaner (although there have been one or two cases where the cleaner has successfully persuaded the maker of the faulty item to pay).
Accessories
Garments, such as coats and jackets, often come with belts or straps that are not attached to the garment and are easily lost (or packed off with the wrong garment if they are not ticketed). Many of these items are constructed from materials that are not common to the garment, such as internal stiffeners, PVC backings and plastic buckles which may harden and crack or (in the case of buckles) partially dissolve in drycleaning solvent and mark off onto other garments. Buckles may be trimmed with papier mâché or polyurethane-type plastics, to simulate various materials including leather and these can fray and deteriorate during cleaning.
In our view, belts and straps should be, in the main, covered by the aftercare label as they mostly consist of or are covered with same material as used in the garment. This means they must be cleaned with the garment to maintain colour uniformity.
Beading
The seamstress failed to secure the ends of the threading which carried the beading, resulting in obvious bands of bare fabric after cleaning.
Beads, diamantes and sequins are potentially very high risk and always demand a careful systematic examination and assessment before cleaning. In particular, check the integrity of the stitching (because breaks in chain stitching may result in many beads and sequins coming adrift). In the case of beaded items and sequins, covering them with light cotton fabric is frequently the only option (other than removal and replacement) to ensure that none are lost (with perhaps manual control of the cleaning process to severely limit mechanical action). The cleaner does of course need to ensure that all beads and any surface finishes are solvent resistant, and also check that there are no projecting metal points on diamante clasps as they can severely damage silk and satin fabrics, even when covered.
When things go wrong –
With the best will in the world, it is inevitable that occasionally garments, their components or accessories will suffer a failure during cleaning and if badly handled, problems can easily end up with the cleaner having to shoulder the blame
Conclusion
It is an absolute disgrace that cleaners are currently having to double guess how to identify and handle unsuitable trim and incorrect labelling on many garment ranges. You might want to keep this issue, together with the May issue of LCN, for future reference on how to minimise risks and claims.
Cleaning reveals insecure beading
Item: attractive designer dress with a decorative band, consisting of rows of tiny beading, stitched around the body.
Problem: the dress came in with the beading apparently secure, but after drycleaning in perc on a delicate cycle many of the beads had been lost, revealing glaringly obvious missing lengths.
Technical cause: examination of the damage in the picture reveals some long loose ends of the original securing thread, together with some very short loose ends. What has happened here is failure, by the maker, to secure adequately the thread ends of the short lengths of beading stitched on to create the broad band. The short lengths now visible will shed more beads if the dress was ever to be cleaned again.
Responsibility: this is a classic manufacturing fault for which a cleaner must always be on the lookout, but the responsibility should be taken by the retailer and ultimately by the original maker.
Rectification: if the maker can obtain some additional beading to match the original, then one of their skilled dressmakers could probably remake the decoration. Otherwise, the owner should make a claim for compensation from the retailer.
Wrong labelling of beaded dress causes havoc
Fault: This heavily beaded dress carried a care label and when cleaned in perc some of the plastic beads (which had a protective coating), partially dissolved and deposited plastic on the dress.
Technical cause: the dress was cleaned using a reduced cycle as required by the care label. Imperfections in the protective coating allowed the solvent to penetrate through to the beads which then dissolved leaving, the coating largely intact. Much damage also occurred because the thread holes through the beads allowed the perc to attack the plastic from the inside, occasionally leaving just the shell of protective coating.
Responsibility: In this case the manufacturer should be taking responsibility, as any trim that is integral with the garment (and cannot easily be removed) should be covered by the care label. However, the cleaner might have to compensate other customers for any plastic mark-off onto any other items in the load, unless they can persuade the maker of the mis-labelled dress to pay. Good luck with that.
Decorative clasp loses its jewels in cleaning
Item: attractive designer jacket in heavy silk, with jewelled clasp.
Fault: during drycleaning in perc (in accordance with the label ), this attractive clasp, stitched to secure the front folds, shed several of its jewels, in effect ruining the jacket.
Technical cause: the adhesive used to secure the jewels was affected slightly by the perc solvent when drycleaned as per the care label. However, the main cause was the stress imposed by the sustained impact with the cage during the cleaning cycle.
Responsibility: the cleaner should share the responsibility here. Although the labelling should have specified a milder solvent and there should have been a precautionary bar beneath the drycleaning circle symbol to denote the need to reduce mechanical action, a competent cleaner should have immediately recognised that there was a very high risk that the clasp would sustain damage if it was not covered or removed before drycleaning. Had it been protected it might have reduced the mechanical impact and also retained any loosened jewels (which would have enabled an inexpensive repair). It has to be said this was a problem that the cleaner should have anticipated, thus saving themselves the time and difficulty involved in responding to a potentially expensive claim.
Rectification: there were no jewels in the button trap and the retailer could not obtain any replacements.
Painted bobbles mark off in drycleaning
Item: Classic designer jacket with colourful painted bobbles.
Fault: When drycleaned in perc on a delicate process, the paint on the decorated ‘bobbles’ came away and marked the rest of the garment.
Technical cause: there are many bright paints which are solvent-resistant, and which are designed to withstand drycleaning. Unfortunately, these were not used here!
Responsibility: the garment maker should take the blame here. Drycleaning using perc is a total immersion process and the solvent has to be used neat so the question of “too concentrated a solution” (as suggested by the retailer) does not arise. Perc was specified by the , incorrectly in this case.
Rectification: unfortunately, none is possible.