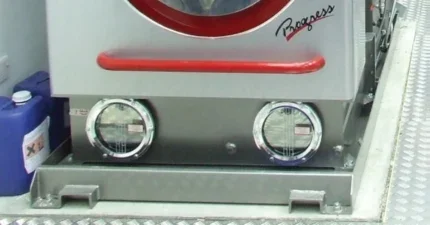
All drycleaning machine operators should monitor their machine on a load-to-load basis, keeping a constant check on issues such as filter pressure, the distillation rate and particularly solvent condition. Maintaining the solvent in good condition is arguably the operators most important task out of many as failure to do so will inevitably expose the business to the risk of claims for greying, shrinkage and distortion. Free water in the machine, characterised by misty, cloudy or milky solvent, is a serious problem and requires immediate attention.
What to look for
Regular load-to-load distillation is a key factor in maintaining the base tank solvent in good condition. Distilling the solvent removes all soluble and insoluble impurities including water. To ensure that impurities in the base tank solvent are maintained at a safe low level, a minimum of at least 2.5 litres of solvent needs to be distilled per kg of work cleaned. The first signs of a developing problem can be slightly misty or cloudy base tank solvent sometimes accompanied by an unexpected rise in filter pressure. Small amounts of moisture in solution with the solvent, (kept in solution by the machine detergent) are very beneficial and facilitate the removal of water-based stains during drycleaning. Provided the filter and discs are in good condition, the solvent in the tanks should remain crystal clear with the base tank solvent normally having a light straw colour.
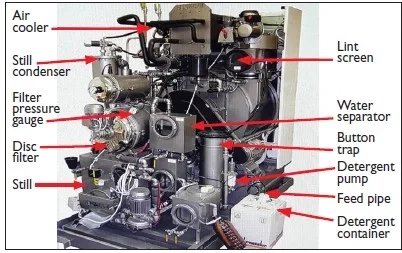
Excessive amounts of water in the system vary from the liberal and random use of general pre-spotting reagents (to which some operators add up to 50% water), to perforated steam heated stills, air heaters or still condenser coils. Even damp foggy winter weather when relative humidity levels consistently remain at well over 90% can increase the moisture regain in garments, and overload the machine detergent with moisture, the excess being precipitated as fine droplets. With larger amounts of moisture/water, most likely caused by one of the above machine faults, the solvent may turn a milky colour; solvent in this condition places animal hair textiles in particular at risk of catastrophic felting shrinkage. Because excess water in the still lowers the boiling point of perchloroethylene, as the amount of water increases the distillation rate increases, this can quickly lead to instability and to the still boiling over (black over).
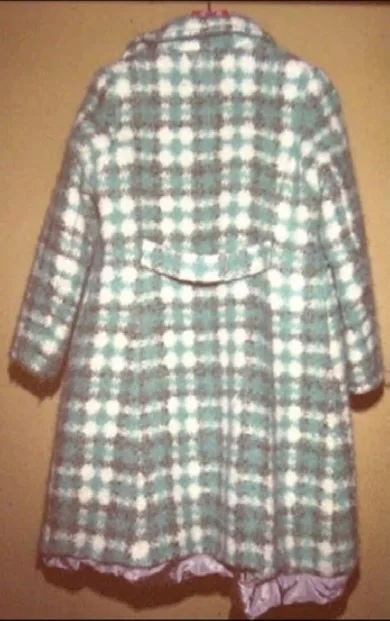
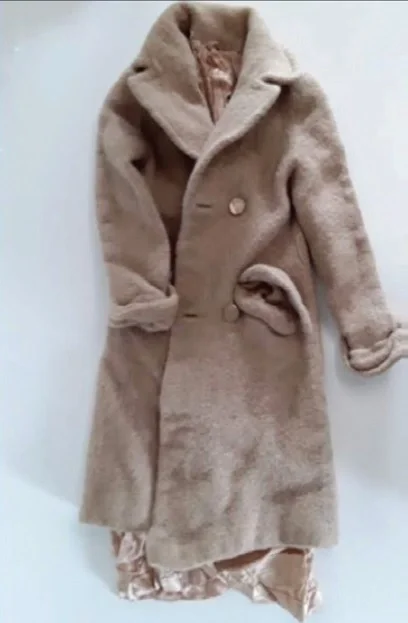
Rectification
Removing excess water from the solvent can at worst be tedious and time consuming or, if you are lucky, and the contamination is limited it can easily be removed.
Water can be removed by either distillation or by absorbing the water from the solvent using bone dry cotton fabric.
Distillation
This is probably the best method if the solvent has become heavily contaminated and has turned milky white. However, under these circumstances, distillation is not always straightforward as larger amounts of water will lower the boiling point of perchloroethylene in the still causing the boiling process to become unstable followed by a “black over”. In order to maintain stable boiling conditions the still heating/ steam pressure will need to be reduced followed by constant observation to ensure that distillation does not become unstable. If a large quantity of contaminated solvent needs to be distilled it may be easier to control stability if it is distilled in smaller quantities as, if a black over occurs, it will be necessary to start back at square one.
Absorption
In cases where the solvent is misty or cloudy, using bone dry cotton fabric is generally the quickest and most economic method of removing the excess moisture. Cotton has the capacity to absorb water very quickly from the contaminated solvent. Be prepared by having available a full load of old stock cotton garments or furnishings, which should be tumble dried until they are bone dry, then immediately transfer them to the drycleaning machine and clean them over the filter with the contaminated solvent followed by extract and dry.