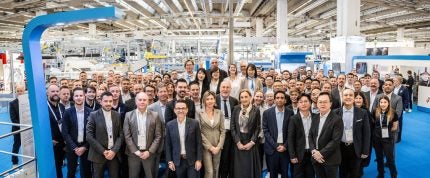
INTERNATIONAL
Jensen-Group looked back over a successful four days at Texcare International 2024, where the company had a busy time on its 1,600 m2 stand. The booth was packed with plenty of innovations for its many visitors to inspect, including advances in laundry automation, robotics, chemical free wash disinfection, a new super-efficient mechanical handling system and a high-speed garment loader along with other new equipment and solutions. The solutions on the stand fully supported Jensen’s avowed mission to, along with laundry businesses, create the future of laundry automation and shape the industry in a sustainable way.
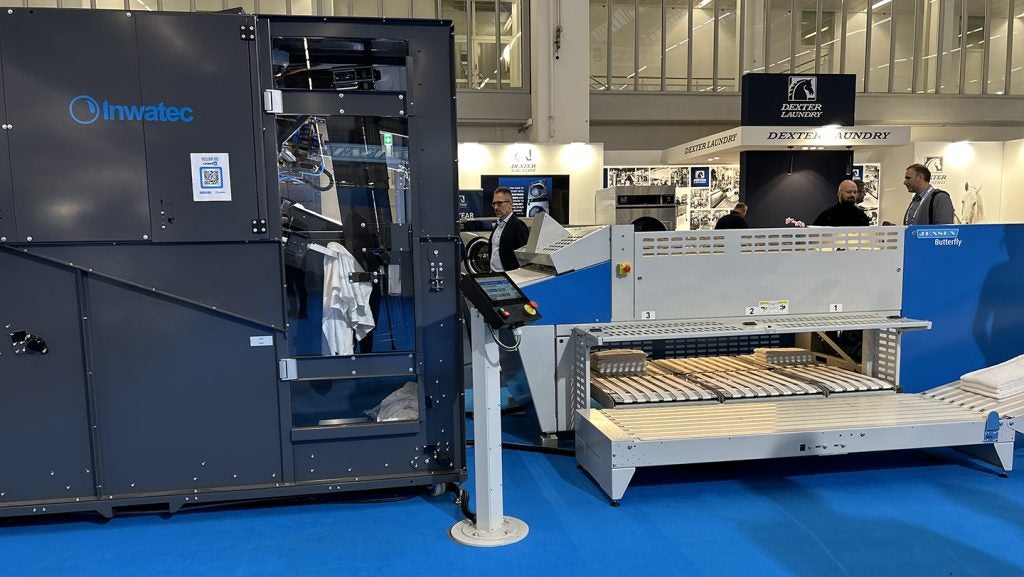
According to Nicolas Gostony, Jensen’s head of marketing: “We showcased various innovative solutions that captured our visitors’ interest, leading to meaningful conversations. Our automated soiled side sorting systems, innovative washroom technologies as well as finishing solutions for flat linen, towels, workwear, and mats were all highly appreciated. In partnership with Inwatec, we presented the latest advancements in laundry automation, receiving positive responses from our customers and partners.”
A standout feature, said Gostony, was the automatic soiled side sorting system with camera technology and AI, showcased in collaboration with Inwatec. “This solution sets a new benchmark for efficiency and ergonomics and is anticipated to become the future standard in every laundry. Over 150 automatic sorting systems have already been successfully installed worldwide, confirming that as suppliers, we offer expertise and innovation leadership unique to our industry.”
Hygiene and efficiency were key topics in the washroom area. UVClean, the chemical-free disinfection method for the double drum section of tunnel washers, was recently granted a patent as well as a hygiene certificate from the renowned German Schubert Hygiene Institute. With UVClean, 90% of the bacteria in the double drum is eliminated after just 30 minutes, going up to 99.9% after 90 minutes. Jensen tunnel washers also claim to feature the shortest transfer times in the industry, thanks to the open drum design without scoops.
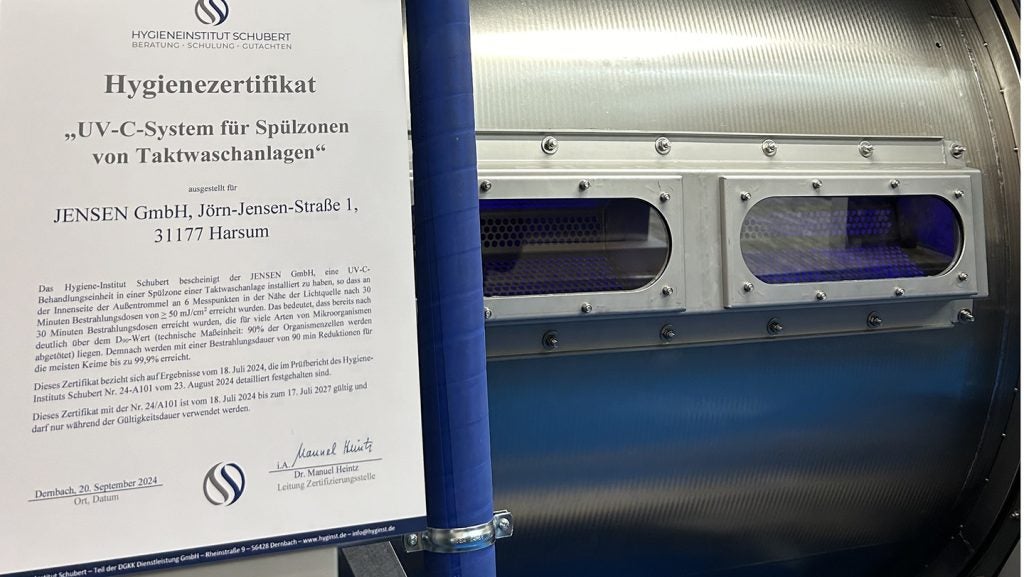
The entire batch is transported to the next compartment in just four seconds by the Archimedean helix. The updated and fresh look of the machine visualisation was very well received by all clients. Every machine can be operated from any other PPC in the wash line thanks to compound redundancy (the ability to operate any machine in the wash line from any PPC). For example, if one PPC fails or becomes inaccessible, another PPC can take over its role. This duplication ensures continuous operation without downtime.
For material handling, Jensen introduced the new RailExpress, a streamlined software solution for full functional control of basic to moderately complex Futurail systems. Laundries can continue to benefit from Futurail’s well-known hardware strengths, like durability, longevity, and increased uptime with a control system that offers excellent value for money. The AutoCalibration feature for Futurail’s sorting bins with its single push button calibration ensures a steady, correct loading of the tunnel washers – with no underloading and no overloading, which can result in incorrect dosing of chemicals, water consumption, and energy. This can significantly contribute to a laundry’s carbon footprint and will soon become an industry standard.
Just in time for Texcare, the new MetriV loading station for garments was launched, a streamlined entry-level workstation that combines a robust design with impressive speed and high capacity. For comparison, it was showcased alongside Jensen’s MetriQ, a high-end loading station featuring built-in comfort and the unique buttons-to-the-front design. “The MetriQ is considered the most ergonomic loading station for garments in the industry,” said Gostony.
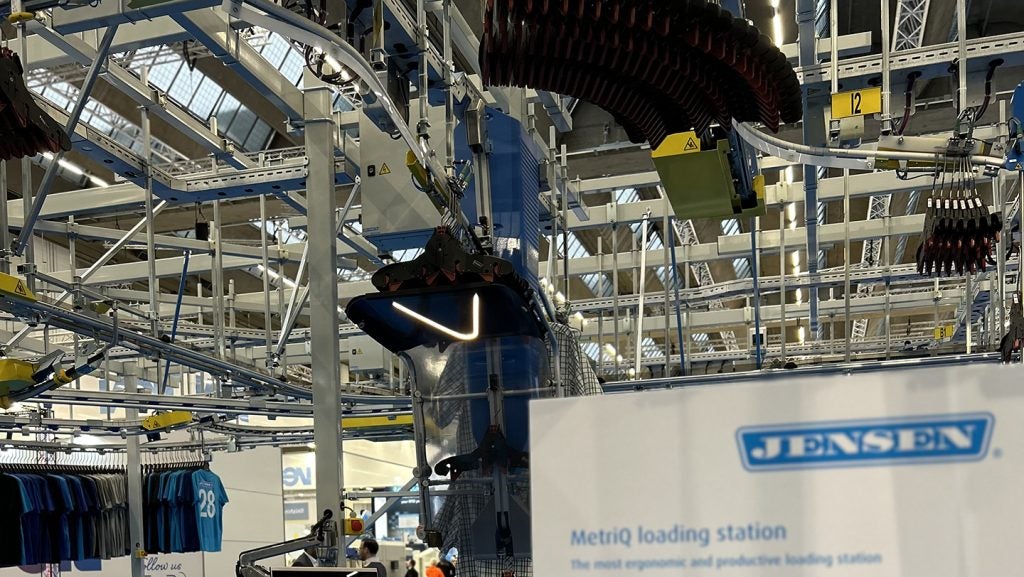
“Other exciting innovations on display were our range of flexible towel feeding systems, including manual, automated and even fully automated solutions: In the automated solution, a THOR.Towel separated and transferred towels to an operator who can speed up the feeding process by up to 83%, achieving 1100 pieces/hour (PPOH) compared to 600 PPOH in a fully manual process. The THOR.Towel feeder is particularly popular in Japan, where workforce is scarce, and this exhibition marks the solution’s first appearance at an exhibition.
The BLIZZ robot for fully automated towel feeding comes with a redesign that allows for more buffer inside the machine, ensuring a stable performance throughout the day – handling 500 small and large pieces in mixed batches.
A significant highlight at the booth were the three state-of-the art flatwork finishing lines, all connected to an impressive Jenway transport and storage system. The Jenway conveyor system equipped with track-and-trace and various sorting and eject technologies connected three ironer lines with Express Pro and KliQ feeders followed by our new Silverline folder with reversing conveyors and space-saving inline stackers. Demonstrations at the booth showed a peak production of 2000 sheets per hour in two lanes on the new Express Pro feeder thanks to four feeding stations for fast corner-less feeding.
“Our exhibition presence was rounded off by an excellent range of services. Visitors were able to find out about services and spare parts at the Aftermarket Desk, while our head of corporate sustainability, Carmela Crippa, engaged in discussions about sustainable solutions, CO₂ reduction, and how our technologies can help customers achieve their ESG goals efficiently and effectively.
“The atmosphere at our booth was highly appreciated by our visitors, as were our booth parties. Our guests felt completely at ease, fully enjoying the unique Jensen spirit. This relaxed atmosphere facilitated valuable connections and engaging conversations. To top it off, outside the booth, our renowned cocktail party with around 800 guests was another memorable moment, providing a perfect setting to network and celebrate the success of Texcare together.
“We are very satisfied with how the exhibition turned out and would like to thank all visitors who came to our booth. Together, we look forward to creating the future of laundry automation and shaping the industry in a sustainable way,” concluded Gostony.