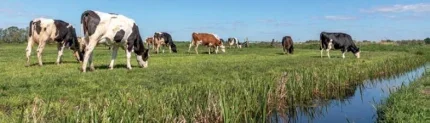
Retail cleaning units in the High Street are already providing valuable cleaning services to dentists, chiropodists, small hotels and B&Bs, care homes (and their residents) and similar healthcare/residential facilities. These have one key requirement in common – they need assured disinfection to protect their staff and customers alike. Until recently, retail cleaners have not really seen this as a big marketing opportunity, perhaps because few establishments have stressed the importance of disinfection and sought justified assurances regarding this. Things are expected to change when finally, the duty of care which organisations are expected to display will become much more important, with assured disinfection playing its proper role. Leading cleaners are now anticipating market demand and preparing to feature this in their promotion and selling. This month we take a look at the different ways of tackling this and, equally importantly, providing the necessary assurances.
Wetcleaning vs drycleaning
It is generally easier to assure disinfection with wetcleaning rather than drycleaning, because a wetcleaning process can employ either implied thermal disinfection or chemical disinfection (or a combination of both). Implied thermal disinfection requires a washing stage involving a minimum of 3 minutes (plus mixing time) at 71C, for example, but high energy costs have made this effectively obsolete. However, the NHS now permits chemical disinfection in laundering, provided this is backed up with an assurance system based on British Standard 14065:2016. We are at least a few years away from this being a requirement for the retail cleaner, but now is the time to be making a start on some inexpensive and practical halfway steps towards this.
Drycleaning has never been regarded as a process which assures disinfection. Perc appears to be lethal to many pathogens but to date, no research data has confirmed this, and organic growth at the watersolvent interface in the water separator gives no assurance as far as a total kill rate is concerned! Hydrocarbon gives rise occasionally to ‘machine odours’, sometimes caused by heavily contaminated work being processed. One might expect the distillation of dirty perc solvent at over 120C to guarantee regular bug removal, but no drycleaning machine is designed to maintain very low bug counts throughout their complicated circuits and it is not reasonable to expect this. Wetcleaning or laundering remain the preferred options for disinfection, and we shall be concentrating on these.
Good soil and stain removal is key to effective disinfection
Bugs need nutrient to breed and survive and protein appears to be the nutrient of choice. Human and animal body fluids are largely protein-based, making it vital to remove these completely from soiled textiles. Wetcleaning and laundering are usually much better at achieving this than drycleaning (in any solvent). This might be why drycleaning horse blankets has caused problem odours in the past.
Any surviving nutrient on cleaned and disinfected textiles could eventually allow breeding from stray bacteria picked up from handling (eg by operatives or wearers), which is why it is vital to remove nutrients from work to be assured as disinfected. Operative hygiene, eg handwashing, can greatly reduce the risk of harmful bacteria (such as E. coli, C.diff or salmonella) going out on finished work, which is always a risk, even though the textiles might have been correctly disinfected in the cleaning process.
Stain removal
Blood, sweat and food stains could be prime examples of protein contamination on finished work, even if they appear to have been visually removed. This is why pre-treatment is important, especially as protein stains can easily become both set and darkened with heat in drying and finishing.
Top tip: protein stains will usually show up better under ultraviolet light – they fluoresce towards pink – highlighting sweat marks and animal slobber that can be invisible in normal daylight or under shop lighting. They will even show up using the small, hand-held UV light used for detecting fake banknotes. This can be an invaluable tool at the stain removal table.
Process design
Implied thermal disinfection (using a very hot main wash) is now regarded as too energy intensive and unreliable to be recommended. Chemical disinfection is potentially more reliable, particularly if the active chemistry providing the disinfection is substantive (i.e. it clings to the textile), providing ongoing destruction of any colonies that start up post cleansing. Quaternary ammonium compounds are good examples of substantive disinfectants. Plenty of alternatives are now available, both in retail and commercially. However, it is important to note that an overloaded machine is unlikely to provide assured disinfection, as overloading prevents uniform penetration of a chemical disinfectant to all parts of every textile.
It is vital to follow manufacturer’s instructions when dosing any chemical disinfectant into a process, because the degree of kill achieved is very dependent on volume and stage time (and occasionally on temperature, even though this might not be very high). If instructions call for a chemical contact time of say five minutes, it is vital to add the ‘mixing time’ to this (that is the time required for the chemical to be uniformly mixed into the load and be in contact with every area of textile in the load at the design concentration). Typical mixing times for small washer extractors and wet-cleaning machines are 3 – 4 minutes but check the machine manual.
Avoiding odours
Odours on finished work are a sure sign of poor disinfection, but they might not develop for some time (depending on how high a kill has been achieved during cleaning and the quantity of nutrient left on the textiles). Complaints of smells that develop in customers’ linen cupboards could be a sure sign of either poor protein removal or a mistake in the disinfecting process.
Poor protein removal can often be recognised by viewing complaint items under UV light. Failures in the disinfecting process often produce a distinctive dank odour in drying and finishing. Canny operatives sniff every batch of towels from the dryer!
Reinfection risks
Those offering assured disinfection need to minimise risks of re-infection during and after drying and finishing. This means making sure clean and dirty flow-paths never cross; it requires, for example, total cleanliness in barrows, other containers and fronts of washing machines. Shipping clean and disinfected textiles requires sealed wrapping or total enclosure in a canvas or similar bag which has also been disinfected.
Guarantees
It is neither wise nor necessary to guarantee complete disinfection – even the NHS only requires a 5log10 kill, equivalent to a reduction of the bug count by a factor of about 100,000. Some bugs cannot be effectively destroyed, especially if they can form spores (which can survive even thermal disinfection). The best a High Street cleaner can do is to state that the textiles have been through the right process using a named disinfectant in a correctly loaded machine. If you need to state the degree of disinfection achieved, then state the chemical supplier’s description of what their chemicals can do and refer any queries to them.
If performance figures are required for disinfection, you could use a dip-slide on say a weekly basis to assess the results in-house. You need a double-sided dipslide which gives viable surviving bacteria colonies on one side and fungal growths on the other. You should aim for zero colonies on both sides and investigate with some urgency if you get more than, say, five or six. The cost of dip-slides is currently under £50 for a box of 10. For larger or more valuable contracts you could secure external certification for your disinfection processes, but this would be understandably more expensive.
Garage overalls start to stink!
Fault: this small drycleaner and launderer processed the overalls from a local bus garage. The overalls looked clean from the wash and were finished in a small finishing tunnel. They smelt sweet on delivery to the garage, but after two days in the locker (still unused) they acquired a revolting odour, about which the customer and staff complained vociferously!
Technical cause: the cleaner’s water supply was found to be significantly contaminated with bacteria which were traced back to the stream from which the cleaner was drawing their water. Upstream of the draw-off point, cows and sheep were grazing the fields through which the stream flowed. Samples further upstream showed low levels of contamination. The bacteria were being introduced onto the clean overalls in the rinse stages of the wash and were surviving in the slightly damp four-thickness seams on the garments (even though tunnel finishing time was 10 minutes at 150C)! The bacteria worked their way out of the seams whilst in the lockers, feeding on the textile finish on the fabric!
Responsibility: the cleaner took the blame here. It was not reasonable to involve the farmer or the garment maker.
Rectification: the cleaner switched to mains water and the problem disappeared.
Horse blankets trigger a problem
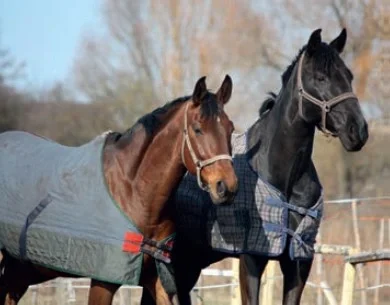
Fault: this cleaner processed a load of soiled horse blankets in a perc drycleaning machine using a 2-bath process, the first bath going directly to still and the second to the working tank. The cleaner then started to get foul, sewage odours on subsequent batches of work. The smell was not eliminated by distilling all the solvent.
Technical cause: horse blankets can carry horse sweat and horse slobber, largely protein based and not solvent-soluble. These can carry a high bioburden of smelly bacteria. The second bath would still carry bacteria and dropping this to the working tank could contaminate the entire machine, allowing bacteria to breed on any lint or other debris, as well as in the water separator.
Responsibility: the cleaner should take the blame here. Drycleaning was not the ideal choice for heavily soiled horse blankets, which can usually be safely processed by wetcleaning or washing.
Rectification: We suggest the still, water separator, button trap, recovery head are thoroughly cleaned followed by a cage flush programme. Then use a biocide product from your chemical supplier to address any remaining bacteria.