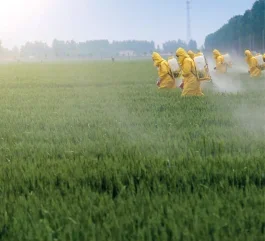
Laundry engineers are usually geared towards problem solving and troubleshooting and they frequently display a broader and deeper range of technical knowledge than other members of the laundry team. Laundry managers who recognise and exploit this usually enjoy higher quality, less downtime and better financial performance than those who treat their engineers as ‘grease monkeys’ with little to contribute. This month we look at just what the shrewd manager of today should be expecting from their engineers and how to recognise this contribution. In doing this it is important to foresee changes in market needs and future demands, especially those involving technical quality and assurance. Let’s see what nimbleness of thought and action is going to be required as our engineers address reducing energy demand and RFID.
Operating cost management
General managers and finance directors are frequently proud of their ability to monitor and manage using Excel spreadsheets, controlling energy costs, for example, to a fraction of a penny. Few realise how much more they might achieve with a brief conversation with their engineer (and production manager). Let’s look at a few examples:
Energy
Traditionally, industrial and engineering workwear customers have sent in garments contaminated with black oils and greases, which used to demand high alkalinity, lots of mechanical action and wash temperatures above 70C. Simple wash formulations based on plenty of sodium metasilicate, and good surfactants did the job quite well. Current energy costs have made this largely unaffordable and modern systems rely on low temperature emulsification of the oils and greases using, among other additives, a targeted emulsifier which has an HLB (hydrophilic lipophilic balance) that matches that of the oils and greases to be removed. This has brought down energy costs for washing quite significantly.
The selection of a low temperature emulsifier is very important and ‘one size’ does not fit all. Food industry garments contaminated with vegetable oils or chicken fats require completely different emulsifiers. In a stark example, a few years ago, of the importance of this, a batch of garments from a chicken processing operation burst into flames in the tunnel finisher. The launderer just had one formulation for oily workwear designed for mineral oils and greases and the inadequacy of this meant that much of the chicken fat survived the wash process. Even the appalling stench when this contract came out of the finisher was insufficient to warn the staff of the impending problem!
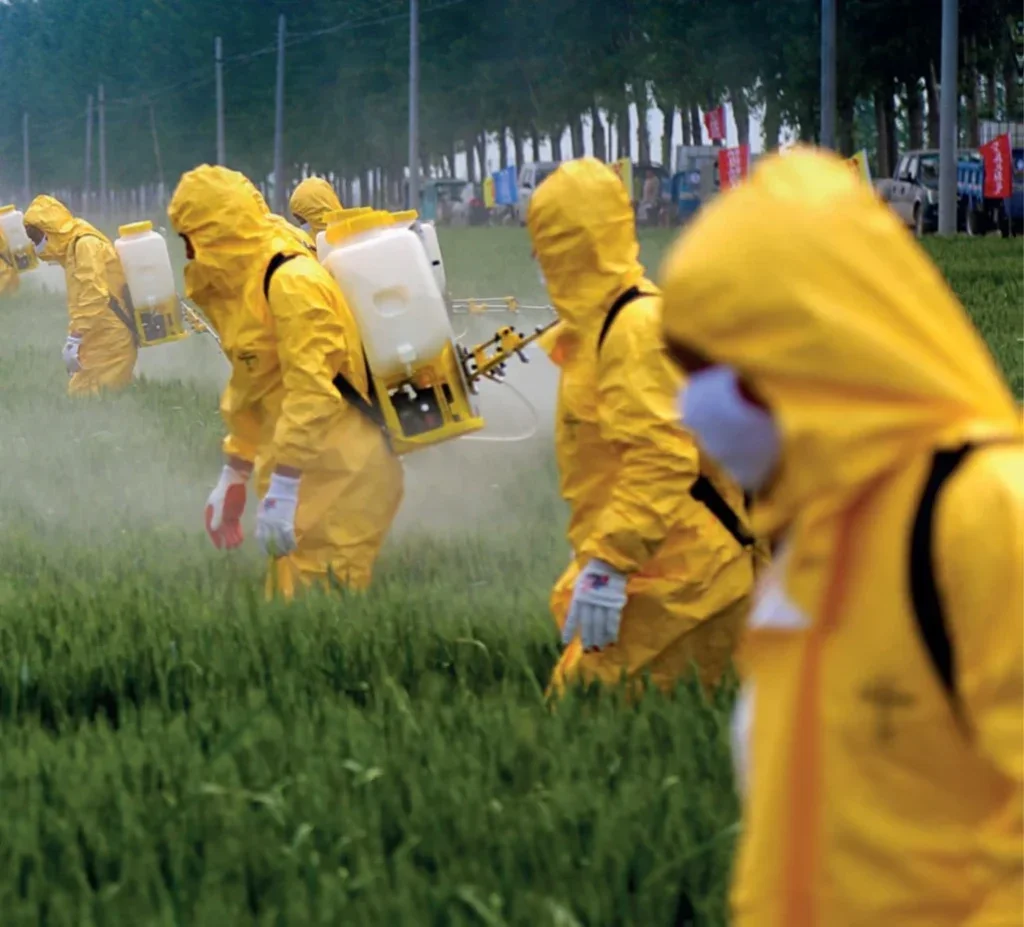
Garments worn by staff in health spas are likely to be contaminated with essential oils, the fragrant ingredients of many spa treatments. These require an emulsifier with a very low HLB value and failure to recognise this is now strongly believed to be the cause of several recent laundry fires. Without the right emulsifier, these oils cling to the fabric and can result in spontaneous combustion of a warm stack of otherwise clean and finished garments. Residues of these oils can also decompose in the tunnel finisher, leading to rancid odours, acid attack on cotton fibres and short textile life. The astute laundry engineer has learnt to recognise the telltale odour symptoms and raise the alarm at an early stage.
Water
The cost of fresh water and effluent disposal is a large and increasing element of processing costs. On workwear plants based on tunnel washers, water consumption is tightly controlled and the variable area flowmeters into the rinse and wash zones can be readily monitored. They provide accurate answers provided they are kept clean. Unfortunately, the same cannot be said of laundering based on washer extractors. Machine manufacturers mostly deliver washer extractors which will work well with the entire range of mains water quality found anywhere in the country. This is not necessarily a good thing, because it means that any plant with better than the poorest quality water is using more water than necessary in the rinses. (The more dissolved alkali there is in the raw water, for example, the more rinse water is needed to avoid galling.) This has enabled wash chemical suppliers to largely dispense with checks on the alkalinity of the final rinse, because this is rarely a problem. If this check were to be brought back, then those with average or good water quality might be very surprised at the savings which could be made. The Laundry Engineer would also find that softener regeneration costs would be reduced, times between regeneration could be extended or the existing softener could support larger washing capacity. Those who have exploited this have obtained useful savings in raw water consumption and in the volume component of the effluent cost.
Quality
Most garment tunnel finishers, if correctly set up, will remove crumple creases and soft folds and some will also reduce pressure creases from normal wear (for example, those from around the seat area of supermarket checkout staff). They are unlikely to improve thermal shock creases (which look like tight crow’s foot mark) from an inadequate cooldown after the hot wash and they will not take out sharp pressure creases formed during the hot wash. The standard answer to these problems was to institute a proper cooldown and to raise the wash dip by typically 25 – 50mm above that recommended for cotton flatwork. Both of these increased the cycle time and raised the water consumption.
Now, with the advent of wash chemistry that enables low temperature washing at say 40C, the cooldown is no longer needed, and the risk of pressure creases is greatly reduced. This means that the cost of washing polycotton garments can be significantly reduced, because not only is there an energy cost saving, but the elimination of the cooldown and reduced wash dip can save considerable water. When this is coupled with the reduction in rinse dips described earlier, the reduction in the cost is even greater.
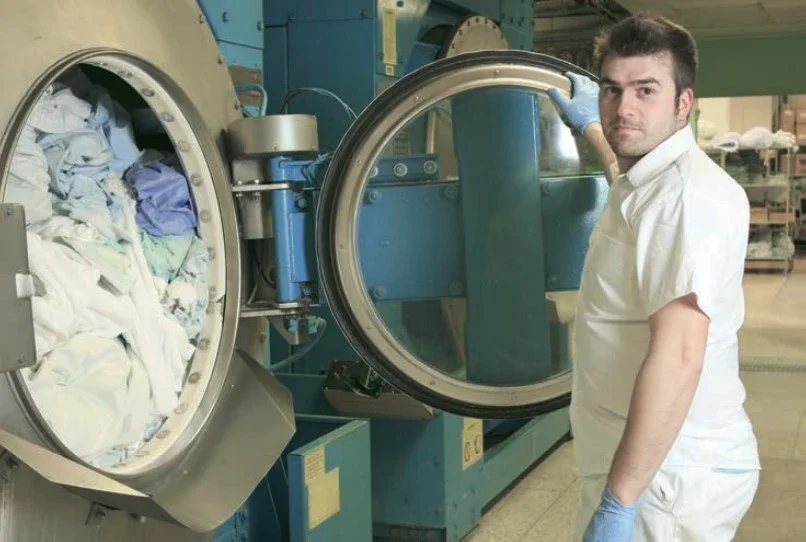
Most of the older traditional high temperature wash processes achieved (whether intentionally or not) implied thermal disinfection to UK NHS guidelines (because they involved a main wash which offered either 3min plus mixing time at above 71C, or 10min above 65C). With low temperature washing there is little thermal disinfection, so a chemical disinfectant may be required. The customer might also want assurance that this is being achieved, and the Laundry Engineer is perhaps best placed to manage this using dip slides or a similar inexpensive in-house method. The best workwear laundries are moving towards simple disinfection assurance systems, based on the Europe-wide standard BS EN 14065:2016, which is already in place at most plants processing healthcare workwear.
Chemicals
Good wash quality depends not on the total amount of chemical additions, but on the concentration of these in the wash liquor. So, if the wash dip is reduced, the chemical dosage can be reduced in direct proportion to the volume of water saved. This not only reduces the chemical cost; it also reduces the amount of chemical contamination discharged to sewer.
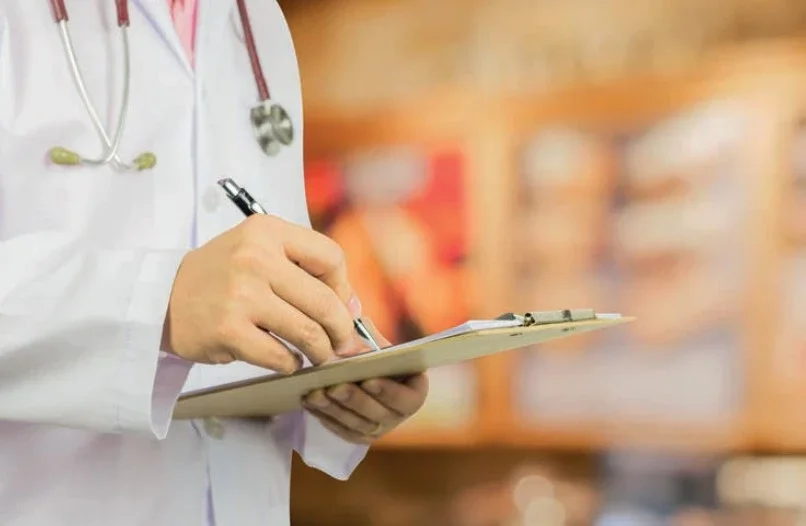
There are real savings to be achieved with each of these adjustments and they are well worth the time taken to implement them in every detail on every machine and on each classification. It really is worth the effort!