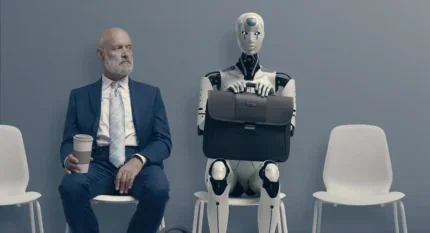
Over the past decade, the industrial laundry industry has undergone a remarkable transformation due to the emergence of artificial intelligence (AI), says Erwin Massen of Laundry Robotics. “This technological advancement has resulted in more efficient processes, improved service quality, and cost savings. The most notable developments in recent years include process automation (determining the appropriate cleaning methods), energy consumption optimisation (streamlining drying times), and quality control (inspection for stains and holes).
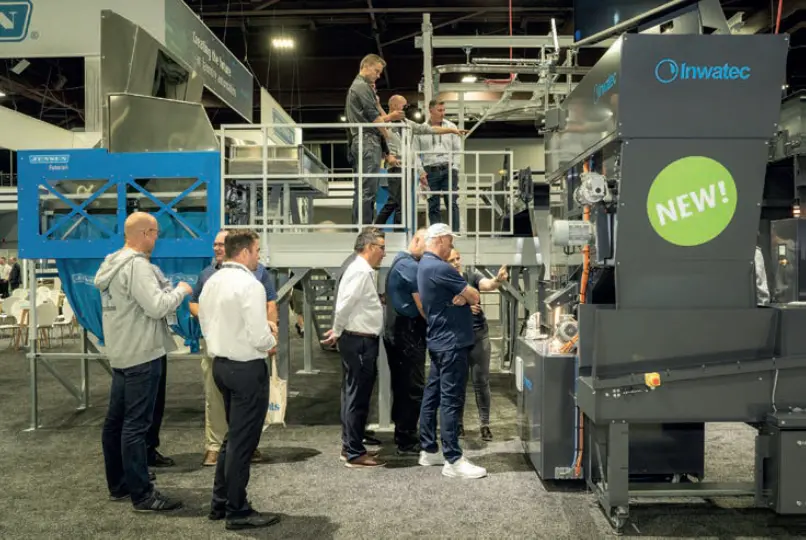
“Automation in the industry is expected to rapidly increase further. More processes will be optimized using AI, enabling laundries to operate more efficiently and strengthen their competitive position. Robotics, coupled with AI, will increasingly play a larger role in industrial laundries. In the coming years, we will witness significant deployment of autonomous robots (such as feeding robots and transport robots) in industrial laundries. In Europe, it is projected that within three years, robots using AI will handle 20% of the towel feeding and the laundry sorting tasks, rising to 80% within seven years. AI-driven quality control will significantly increase due to this robotic integration. Subsequently, there will be a shift towards more sophisticated robot solutions capable of executing complex tasks.
“Sustainability will remain a central theme in the industry, with AI being leveraged to further optimize resource usage. From reducing water consumption to minimising chemical waste, technological innovations will be harnessed to diminish the ecological footprint of industrial laundries.
In conclusion, the rise of AI has transformed the industrial laundry industry over the past decade, and the pace of change is expected to accelerate in the coming years. Investing in AI and robotics now will enable industrial laundries to enhance their efficiency, improve service quality, and contribute to a more sustainable future. Furthermore, it is essential to remain competitive amidst these impending developments in robotics and AI.”
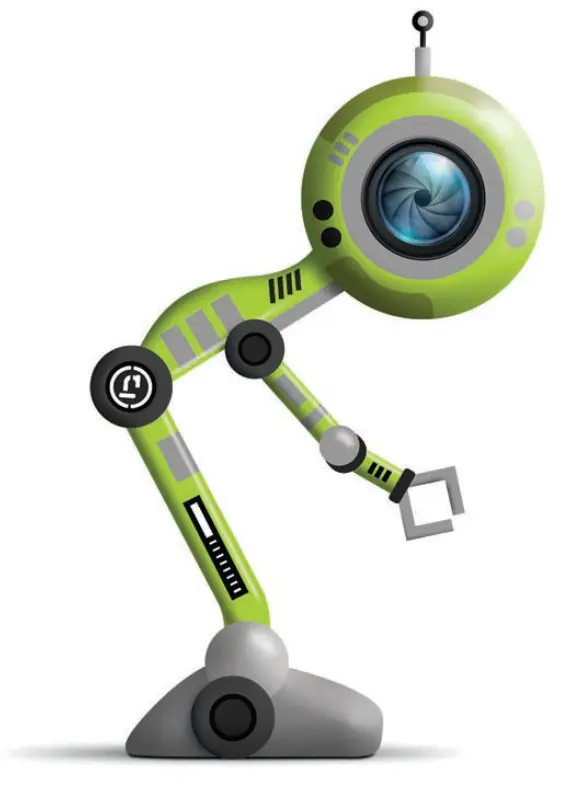
Laundry Robotics exhibited its initial version of the Robin automated towel system almost a decade ago and has moved from strength to strength in the years since.
The machine has changed dramatically since those early days with the company working closely with its clients to improve upon that original model. And not wanting to rest on their laurels it then released a baby brother for Robin, called Roy, at Expo Detergo in 2022.
Philip Ghosh of Biko UK, distributor for Laundry Robotics in the UK and Ireland, says: “With Texcare fast approaching in November, I am looking forward to seeing what fresh and exciting ideas will be on the stand.”
Organiser of Texcare 2024, Messe Frankfurt, says: “Despite the rapid advances in automation, the textile service industry is inconceivable without human beings. Their cognitive skills are required, in particular, for coding, individualisation (applying name badges or patches), length adjustment and repair, as well as for cleaning private laundry. In many cases, a trained eye is often faster than cameras and artificial intelligence when it comes to quality control and assessment. However, as such activities quickly lead to fatigue, it is likely that the next wave of automation will be in this area of textile care.” (See page 7 news story.)
Andreas Langer, Kannegiesser’s marketing manager, agrees wirth Messe Frankfurt’s statement as he explains the reasons behind the development of Kannegiesser’s fully automated dry laundry line: “Due to fatigue, the operator’s input performance naturally fluctuates and decreases over the course of a shift. Automation prevents input from becoming a bottleneck and slowing down the laundry process. This arduous task is performed by stateof- the-art equipment. Working with advanced technology, such as robots and intelligent control systems, has another advantage: it makes it easier for a modern laundry to attract techsavvy employees and specialists who find working with innovative and futureoriented technologies exciting and want to be part of a modern company.”
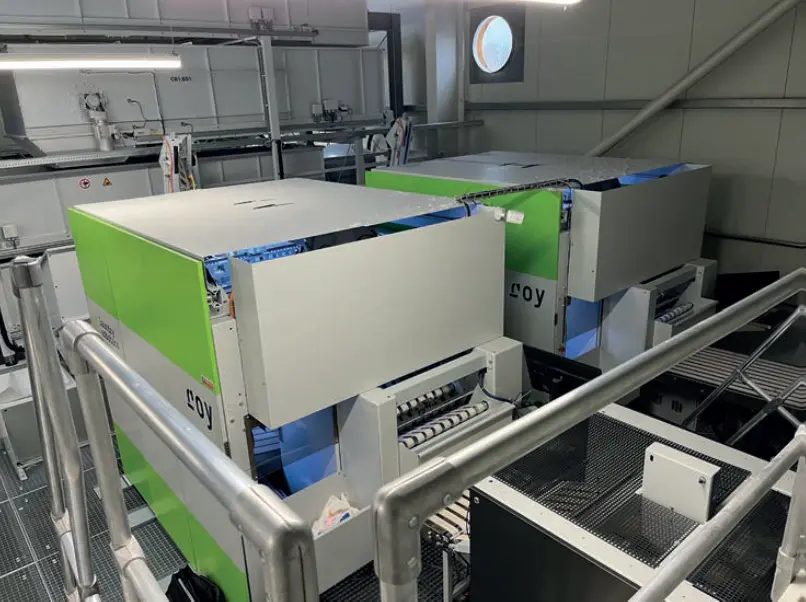
Kannegiesser says, for example, AI results in an hourly folding rate between 600 and 700 items, depending on the variety of items to be processed. For example, a person is still faster than a machine when folding smaller items of laundry, such as flannels.
Jensen-Group has long championed the benefits of robotics and artificial intelligence having tied up with innovative AI developer Inwatec some years ago. Now Inwatec is very much part of the Jensen family. Inwatec’s ODIN.Xray scanner is capable of scanning and subsequently rejecting garments containing harmful foreign objects, such as pens or needles. To achieve the best possible results, cutting-edge AI software is utilised to continuously train the machine according to the specific requirements of each laundry. The quality of detection ultimately depends on the types of garments being scanned. Jensen has collected millions of images, which are segmented into samples for training a neural network with approximately five million of those samples. Jensen’s goal is to provide the neural network with enough samples to have seen most, if not all, items that pass through a laundry. Neural networks excel at identifying items they have encountered before. Hence, we aim to provide as many examples as possible of what accepted items should look like (buttons, zippers) and what foreign, unwanted objects (knives, scalpels, scissors) should look like. Detecting metal is relatively straightforward, but identifying plastic items is more challenging.
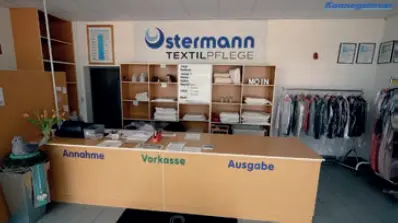
“The initial version of ODIN did not rely on AI. By transitioning to normal computer vision with AI, we have increased the detection rate to up to 99%. Taking a picture with an X-Ray scanner is not a complex task, but finding all the undesired items while accepting items belonging to a garment is. The AI in ODIN ensures the system differentiates between laundry items that need to be rejected due to the presence of unwanted objects.’
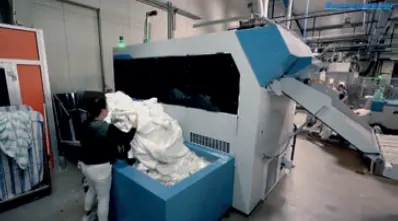
The HEIMDAL.camera is built upon AI to sort products based on their visual characteristics, such as colors, patterns, textures, and even size. CouUpled with intelligent software, HEIMDAL can distinguish between different types of laundry articles. Each project receives its unique set of data, which requires training for the specific sorting composition and product portfolio. Currently, we have various systems in operation for workwear, linen, and mixed products. Even without RFID, HEIMDAL can achieve higher sorting accuracy than manual sorting.
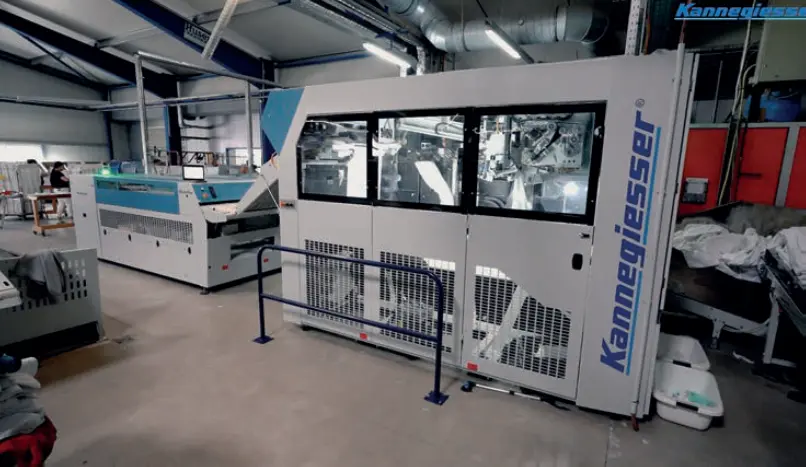
The input for HEIMDAL is also an image, but unlike the X-Ray image, it is a real color photograph. The system is similar to ODIN in that it employs a neural network to create a fingerprint of the item, enabling precise identification, distinguishing between items such as small towels and large towels.
FROM LAUNDRY CART TO ROBOT
“I believe that laundries will not be able to survive without robots in the future. All laundries are experiencing a shortage of staff,” says managing director Bernhard Ostermann of Ostermann Textilpflege, based in Esterwegen in north-west Germany, which has been in business for almost 60 years. The laundry’s recipe for success includes a constant drive to modernise. “Over the decades, we have always pushed ahead with further developments.
“The next step is robotics: since 2023, the automatic dry work line by Kannegiesser has been the heart of the laundry. The special feature here: Pre-sorted laundry batches are loaded manually from the laundry trolleys into the dry work line – without a fully automatic monorail bag storage system.
“The robot has the advantage for us that we are much faster in production. This means that the items come out of the machine more continuously,” says Bernhard Ostermann. “At 700 items per hour, the output meets Kannegiesser’s specifications.” He adds that the system achieves this output, for example, when processing mixed batches for hotel customers with hand towels, shower towels, bath towels and bath mats.
After drying, the batch is pre-sorted manually: Employees sort out items that the robot cannot process. For example, these are fitted sheets and incontinence pads. The pre-sorted batches are then loaded from laundry carts into the automatic dry work line, which then feeds, folds, sorts and stacks each item fully automatically.
Finally, the finished stacks receive packing slips via the Kannegiesser Pack & Label system. “With the Pack & Label connected, the robot can develop its full potential,” says Bernhard Ostermann. In this way, he adds, the laundry can prepare its goods directly for shipping.
Of course, the dry work line only unfolds its full potential in fully automatic operations with modern monorail bag systems. However, Ostermann Textilpflege shows that it is also a perfect solution for a semi-automatic operation with laundry carts.