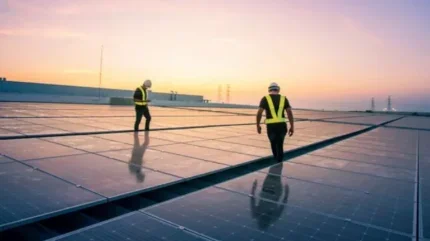
Whether people are embracing sustainability in a sincere attempt to save the planet; to ensure they fill CSR requirements; or their real motivation is more Scrooge-like – to keep more money for themselves – ultimately the result is beneficial for all.
Over the past year we have seen textile care operations, manufacturers and suppliers adopt the latest technology to achieve more sustainable outcomes. ‘Sustainability’ has become such a buzzword over the past years that it seems to used for any development including changing the design of a switch. OK, that might be a bit cynical, but the thing is, that in this day and age we need to be flagging up and pointing the finger at what is NOT sustainable rather than what IS. Sustainability is now the norm, not the exception.
Let’s look at some examples of recent initiatives that can really make a difference in the drive towards Net ZERO.
The Future of Energy seminar presented by the Worshipful Company of Launderers in London at the tail end of February saw expert speakers discuss the future provision of energy, concentrating on alternative sources to fossil fuels that can save energy, and even generate additional income for businesses.
Andrew Moore, UKSOL, reckons solar PV could point the way forward for big laundries with large roof spaces which could use them to enjoy lower electricity prices.
Moore, the founder and CEO of UKSOL, the leading British Solar PV panel producer and exporter has built up a wealth of experience with 15 years in renewable energy and is a solar entrepreneur specialising in emerging global solar markets, including Africa, Asia and South America. Andrew is an export champion for the Department of International Trade and has a vision to build a megawatt solar panel manufacturing plant in Britain as currently there is no large scale solar panel manufacturing here.
In the developing world, solar PV is “power to the people” he says as it is so much cheaper than building power stations .“In Europe we are colder than Africa, of course, but solar PV is actually more efficient at lower temperatures and suits our climate. Solar PV is not a new technology and is currently being used on Mars powering Rovers and has been used to power satellites in space for decades.”
“Solar PV can be deployed for large factories on their roof space. We need good software to calculate the benefits. Ask an installer to generate a report on location (ie., Scotland or south coast?) All can impact on results as can pitch of roof, temperature, shading – shadow from chimneys and trees can dramatically reduce output.
“Why are you buying a system? To save on electricity bills. Also, as a back-up. This is now on the agenda as we could have blackouts and brown outs like back in the 70s. Solar PV can provide a store of energy when you need it.”
Lithium batteries are available but are more expensive than the previous units, but are better and more efficient. However, bear in mind that batteries are expensive and although installers will quote for them in the installation they are optional. The National Grid acts as a battery as any excess production can be harvested and you get reduced bills. “A solar PV system once installed basically plugs into your power supply in the building and you use the power from the panel to run the building.
“The installation should last at least 30 years. Once a system has been installed almost no running costs are incurred as they have no moving parts,” said Moore.
“How does it help your business? You won’t be totally self-sufficient but will really significantly reduce the amount of power you buy from the National Grid. It’s a hedge against rising prices. Other pluses for going the solar PV route, according to Moore, are that it will help in achieving Net Zero, “you can talk to your customers about it and put it in your marketing matter. We don’t know what is going to happen with tax on energy. It could well be helpful there”.
‘We are colder than Africa, of course, but solar PV is actually more efficient at lower temperatures and suits our climate ’
“You can even sell excess power to other people/businesses or back to the National Grid,” Moore said, adding: “Do ask for a report. MCS is the Government body set up to manage renewables installers. You will definitely need an MCS approved installation over 50kw, so do check this.” https://youtu.be/grmOLlNbUmE
Solar pioneer
One laundry company in the UK that has gone the solar route is Micronclean which successfully commissioned its recently installed solar panels on the roof of the company’s plant in Louth, Lincolnshire. The solar array of 577 panels was installed by NerG of Lincoln and over the course of year will supply 20% of the Louth plant’s annual electricity requirements.
Micronclean employs over 400 people across the UK with most of these being based at the three main production sites in Lincolnshire. The Louth site is home to one of the most technically advanced ISO Class 6 (GMP Grade C) cleanroom laundries in Europe, with the capacity to process more than 120,000 items a week.
The Micronclean environmental and sustainability strategy sets out Micronclean’s ambition to be “the most sustainable specialist textile and cleanroom consumable business on the planet. This ambition is supported by three pillars: our climate, creating our circular economy, and; our people and communities.”
In Year 1 of the strategy under ‘our climate’ Micronclean committed to reduce its carbon emissions by 5%. As part of this the company has built on its recently signed Renewable Energy Guarantee of Origin (REGO) electricity supply contract by funding its own solar array on the roof of the Louth facility. The installation and commissioning of the 577 panels that cover 70% of the roof at Louth was conducted by Lincoln-based firm NerG.
Luke Worral, business development manager at NerG says: “We are really proud to have worked with Micronclean on this large Solar PV project, helping to mitigate over 42 tonnes of CO2 annually which is a great way to contribute to their MicronGreen Strategy.”
Sophie Harris, associate director QHSE at Micronclean, adds: “We take our commitment to the environment very seriously and the successful completion of this project is another sign of this. Over the course of a year the solar array will deliver 20% of the electricity that the Louth plant consumes and is another bold step on our pathway to zero carbon emissions.”
On the laundry floor…
So, what more can be done to reduce energy costs and emissions? Competition between laundry equipment manufacturers is a healthy thing here, as they are vying with one another to produce the most efficient products. Considering what they are up against in an industry that has traditionally needed to generate heat and use copious amounts of water they have done an exemplary job.
Washer-extractors
Domus washer-extractors offer a high G factor for more efficient spinning. It claims its DHS washer-extractor with its 500 G spin can reduce topical drying times from 45 minutes to just 25 minutes and offer a 50% energy cost reduction, low water consumption via Domus TOUCH II technology. On a 100% cotton towelling full load in a 28 kg washer its figures show consumption of just 6.6L/kg including pre-wash, wash and three rinses.
Water savings are achieved by using the inbuilt weighing system which can make significant savings on part loads. Chemicals savings, meanwhile, are achieved via the TOUCH II microprocessor which allows configuration of the machine to levels to achieve chemicals savings as well as water and energy savings, no matter the load level. The lesser the load, the more the savings.
Water recovery is via Domus’ ECOTANK and ECOTANK XL. Ecotank XL is a new centralised tank that can be connected to one or more machines. Each tank is 1,000 litres, with 1-3 tanks available.
“In a DHS-80C TOUCH II washer we can achieve up to 56% water savings thanks to ECOTANK XL if we load 60% of the capacity with towels, in the washing machine alone it will use 656 litres but in a washing machine with Ecotank XL it is just 288 litres,” says Colomer.
As for energy, Domus claims it can achieve 12% electricity savings with the same load and ECOTANK XL. Washing machine on its own will use 21.37 kW/h and with the washing machine hooked up to an Ecotank XL you get 18.80kW/h, says Colomer who adds that the data is based on tests with an 80kg washer with a 60% load with towels.
MAG Laundry Equipment washers come with capacities ranging from 25kg to 150kg. The company claims that its new quicker and quieter equipment could reduce utility bills by up to 60%. “There is a staggering difference when you compare highly efficient laundry equipment to inefficient machines that are wasting energy on every cycle,” says the company.
“The benefits of energy efficient laundry equipment can be seen in many aspects of life. One of the most important benefits is protecting the environment. Another important factor is reducing waste and increasing profits which is an important part of any business.”
The latest models launched by MAG Equipment include new drum capacities of 25kg, 39kg, 50kg, 65kg, 85kg and 100kg. Other heavy-duty, commercial and industrial models are available from 8kg to 150kg to help make quick, clean, efficient work of your laundry.
Simple to use with advanced features MAG’s washing machines and tumble dryers can recycle water, retain heat and significantly reduce washing and drying times, says MAG.
Meanwhile, Generating up to 400+ G-force extract speeds, Girbau’s HS-Series soft-mount washers outperform industry hard-mount washers by removing more moisture from every load and slashing dry time by up to 50 percent. This allows for the completion of more laundry kg per day using less energy, labor and natural gas.
Dryers
Is steam generation still necessary? Do we still need dryers for bed linen when water extraction is so good at washer level linen can go straight to the ironer line? Do we just need them for fluffy towels nowadays? We got answers from the big players in the market.
Edouard Colomer, export manager at Domus says: “At Domus we like to explain the high efficiency of our products: low water and chemical consumption and great energy savings throughout their lifespan. And how do we do that? It is not a simple statement, but differently from other brands, we supply numbers and figures. We even send a leaflet and a real calculator to them.
“You can see our calculator videos, for example this one where we show clients that a Domus 60kg gas dryer can save 121.000 kW a year, thanks to the Air recovery system, thermal insulation, and intelligent moisture sensor.” https:// youtu.be/Rb423CxlN2Y
Kannegiesser has big claims for its latest dryer technology, saying: “Technology and innovation make the difference. A difference that our customers should be able to see and feel first hand. As for our transfer dryer PowerDry, the difference is called CareDry and Eco2Power.
“CareDry is a special drying program that reliably preserves the quality of terry cloth. It prevents overdrying and thus scorching and greying of the textile fibres. CareDry meets the highest requirements for softness, whiteness or colourretaining.
“Eco2Power is a process control that combines lowest energy consumption with maximum performance. Due to the optimal use of circulating air, less heat supply and thus energy is required. At the same time, the automatic control system reduces process times and allows greater performance.
Girbau has added a new range of dryers that it says can make a sifgnificant reduction in gas use. “Comparing Girbau’s ED260 with our previous generation GU030 dryer, we are typically seeing a saving of between £2 and £3 in gas use for each full day of operation,” says Peter Rankin, managing director of Girbau UK.
Available in six models from 14.5kg up to 62.5kg, ED series dryers ensure all items including delicates are dried safely, uniformly and cost-effectively. A built-in humidity control system automatically senses when clothes are dry and activates the cool down process. Unique to Girbau, the stainless steel Care Touch drum features recessed vents, no sharp edges and a highly polished surface to protect and preserve delicate fabrics.
The wide opening door makes loading and unloading quick and easy while a large capacity lint filter and easy access to drive system makes maintenance simple..
Complete aisle solutions
Kanegiesser believes laundry operators looking for a revolutionary solution with maximum efficiency, minimum energy consumption and simple principles with phenomenal results can find it through the combination of its own PowerSwing washer-extractor, Lift Shuttle Conveyor and PowerDry dryer. This complete wash aisle solution perfectly balances cost-savings, performance and hygienic laundering in one package, says the company.
The PowerSwing has am optimnised loading and unloading system makes use of the rotatable inner and outer drum, allowing for efficient and fast loading and unloading so maximum use of the drum volume is achieved, offering larger loading quantities. Additionally, due to the variety of layout options available, the PowerSwing has seamless integration into any laundry facility, with loading possibilities such as a simple inclined conveyor, cart dumpers, bag systems and more.
The Lift Shuttle Conveyor offers the highest effciency by reducing idle times and allowing machines to operate quickly and efficiently, thanks to quick acceleration and braking, using highend speed, and through intelligent signal exchange between the machines. This allows for a tailored link between PowerSwing washer/extractor and PowerDry dryers for the fastest possible laundry feed.
The PowerDry’s ECO2power option maximises efficiency and ensures minimal energy consumption with low required energy supply, high air recirculation proportion, optimal laundry fall curve, and exact dry-point recognition. Kannegiesser says PowerDry is the perfect solution for laundries seeking to maximise their efficiency, reduce energy costs, and ensure a sustainable solution. This successful combination of machines ensures the perfect balance between cost-savings, optimal performance and hygienic laundering for a complete wash aisle solution.
Jensen is a one-stop-shop supplier to the heavy-duty laundry industry, and has a longstanding tradition of integrating sustainability aspects into the machine development and in the way it does business. It says it at increasing the competitiveness of its customers, and at the same time, their sustainability.
It, too, has a whole aisle persective with its CleanTech concept which drives down water ansd fuel use. The objective of the Jensen CleanTech concept is to increase the efficiency of the primary energy and to reduce its use with gas-operated laundry machines.
When developing laundry machines, the Jensen- Group concentrates on achieving high performance and minimum energy and water consumption. In addition to direct gas operation, this involves the integration of internal energy and water recovery systems. When the machines achieve higher process temperatures, the drying and finishing times are dramatically shortened, which increases productivity.
It claims record figures in CleanTech laundries using Jensen technology:
- Tunnel washer Senking Universal consuming 1.6 l/kg or 0.2 gal/lb water
- WR Dryers: 0.95 kWh/l resp. 1,474 btu’s/ lb
- Jenfeed Express: 1800 pcs/h
- More throughput, higher availability: 0.8 kWh/kg resp. 1,365 BTU’s/lb of linen Jensen uses Globe software by Gotli Labs, and says it can prove its statements with transparent figures.