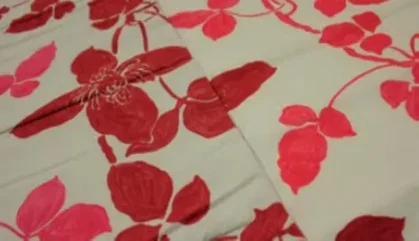
While greying (redeposition of soil or colour) can be a problem in drycleaning, wetcleaning and laundering, it is because of the lower cleaning and suspension properties of drycleaning detergents (when compared to products used for water-based processing) that greying tends to be more of a problem with drycleaned items. All colours can be susceptible to discolouration from greying, but special care needs to be taken when drycleaning pastel shades and white items. During wear, greasy particulates from atmospheric soiling build up in textiles and during cleaning these are easily released from fabrics by the solvent – all drycleaning solvents are good at dissolving oils and grease. However, once particulates are released, and come into direct contact with the surface of clean textiles, in the absence of the greasy layer some particulates may become firmly attached by electrochemical forces to fibre surfaces, while others may be embedded in textiles (especially in cotton, linen and wool, which have irregular fibre surfaces).
In addition to redeposited particulates, greying can also be caused by loose or extraneous dye liberated from items by solvent action in the machine. Most textile dyes are specific to a particular fibre type or in some cases similar fibres, and many are substantive (have an attraction for the textile). This explains why, if a colour run occurs, it may only affect one or two items in the load, leaving the rest untouched.
Some textile fibre types are particularly susceptible to greying, polyester being a prime example (together with cotton and other cellulosic fibres); so, the removal of greying can, to say the least, be problematic. Good cleaning practice and solvent management are therefore essential if cleaners are to avoid the serious consequences of greying in drycleaning. Many cases of greying are directly related to poor classification.
Classification
Dark and medium items are more likely to be carrying heavier soil loadings than lights and whites and in addition, darks and deep dyed shades, in particular, are much more prone to dye bleeds. So, any lights, whites and pastel shades will be seriously at risk of greying if they are cleaned with darker classifications.
It is therefore critical that items are at least sorted into the following:
- Darks
- Mediums
- Lights
- Whites
- Delicate items
- Specials (household, leathers, dye bleeds etc.)
These are the minimum classification groups if the greying of whites and pastels is to be avoided.
In addition to the above, the cleaner needs to ensure that garments are also correctly sorted in respect of fabric/ fibre type and the weight of individual garments. A common classification error is the inclusion, in a dark load, of a black item with white trim. This frequently leads to the discolouration of the white component. Make no mistake, if this happens, it is the cleaner’s responsibility!
Good solvent management
Solvent clarity and purity is essential in mitigating the risk of greying. The use of the hybrid cleaning process will, if properly monitored along with regular machine maintenance, ensure the machine solvent is maintained in good condition.
Typical hybrid process, using perc solvent, to minimise greying:
- Base tank solvent charged with 3 – 5 gm/ litre of drycleaning detergent.
- 4 min circulating dip drawn from base tank, drained and extracted to the still.
- 8 min wash over the filter taken from distilled tank, with addition of 3 – 5gm/ litre detergent.
- Drain and extract to base tank (which ensures that the detergent charge in the base tank is consistently maintained)
- Dry as normal.
The total cleaning time of 12 minutes (the time items are actually tumbled in a dip or flow of solvent) is the minimum recommended for cleaning robust items in perchloroethylene. We would suggest an extension in cleaning time from 12 to around 20 minutes for those cleaners using hydrocarbon solvent.
In order to maintain the base tank solvent in good condition and prevent the build-up of soluble impurities such as oils, tars, waxes and free fatty acids, it is essential that at least 2.5 litres of the base tank solvent is distilled per kilogram of work processed. Failure to ensure an adequate volume of distilled solvent exposes the cleaner to substantially increased risks of greying and unpleasant odours in drycleaned items.
The above process is suitable for darks, mediums and lights but in order to reduce greying risks to the minimum it is essential that filtration is fully established (producing crystal clear solvent) before the cage inlet valve opens. Check colour and clarity of the solvent in the filtered solvent sight glass – see the solvent flow diagram. ‘Delicates’ will require reduced cleaning time and reduced mechanical action.
Cleaning whites
We have often found cleaners who have had problems with white items, clean them in a single static bath of distilled solvent. While the solvent may be perfectly clean, it only remains so for a few seconds, until soil starts being removed; the garments are then being cleaned in dirty solvent. At worst this can result in serious greying from a single clean.
Even the best drycleaning systems result in a minute but measurable amount of redeposition, which may build up over a number of cleans, until it eventually becomes noticeable to the customer. Provided the item can be safely wetcleaned/ washed this is often the best option in order to maintain an ongoing high standard of whiteness. Where drycleaning is necessary, it is critical that, to avoid particulates being redeposited, they are quickly removed from the vicinity of the garments. The following cleaning process can provide a good process structure for white items, with appropriate adjustments for sensitive garments.
- 6 min. low-dip filter wash, drawn from the base tank (the solvent must be no darker than a very light straw colour).
- No additional detergent is needed, because in the hybrid system the base tank is already charged at 3 – 5 gm/litre.
- Drain and extract to still.
- 3 min rinse in distilled solvent.
- Drain, extract to still (provided low dip used in first stage there should be plenty of room) and dry.
- After unloading, balance the base tank solvent with distilled solvent and add detergent (3 – 5 gm/ litre).
Top tip: It is vital that the filter is producing crystal clear solvent before the cage inlet valve opens and cage rotation starts. Use the diagram to find the filtered solvent sight glass on your machine.
Detergent
It is almost beyond belief but there are still cleaners around who do not use detergent in their machine! Drycleaning detergents are no less essential than the detergents used in laundering. Failure to maintain correct detergent concentrations in the machine, will not only reduce levels of soil and stain removal but significantly increase the risk of greying. In addition, this will further expose the cleaner to a heightened risk of shrinkage and distortion.
Detergents have a critical role to play in drycleaning and in addition to promoting the removal of particulate soils, once removed they also hold these in suspension in the solvent and substantially reduce the risk of redeposition on the fibre surfaces (where, in some cases, prove impossible to remove)
What is not always appreciated is that the detergent also has an equally important function in the removal of water-soluble soils and stains. Drycleaning detergents have the capability of taking safely into solution the small amounts of moisture liberated from some textiles and also the moisture from water-based spotters and general pre-spotting reagents. Moisture held in solution is safe and promotes the removal of water-soluble stains and soil. However, free moisture within the system (characterised by cloudy solvent) increases exponentially the risk of greying and shrinkage. This is because free droplets of water are particularly attracted to cellulosic textiles, carrying, with them dirt and soil, while animal hair textiles are exposed to a high risk of felting shrinkage. It should now be obvious that not using or economising on detergent can lead to a host of problems.
Recovering greyed Items
Whatever the cause, if you are very lucky, re-cleaning the greyed item on its own (using the foregoing process for whites) may resolve the problem; but in many cases washing or wetcleaning, using an appropriate detergent, stands the best chance of success. In the case of contamination with loose dye, it might be appropriate to utilise a proprietary colour run remover.