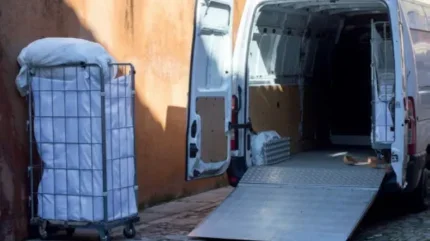
This series of three articles highlights the basic areas which the engineer must cover, which might help to design a training plan for what is needed in each individual plant. In later editions we shall be looking in detail at every aspect of the engineer’s role. Getting this right is fundamental to meeting cost management targets, minimisation of energy (and water) consumption and labour productivity. There are still considerable benefits to be gained in many laundries.
Utilities
- Water quality is fundamental to laundering quality and the engineer has to ensure consistent softening down to zero hardness and the routine daily checks that are needed. Checking hardness immediately after softener regeneration is essential, but so is the occasional check immediately before regeneration (to ensure that the resin is still functioning correctly).
- Iron in the raw water (which can poison the softener resin) is an increasing problem in many regions, as drought conditions continue to concentrate impurities. Iron will catalyse (accelerate) the breakdown of cotton if sodium hypochlorite bleach is being used, and it will promote premature greying of white work. Getting residual iron consistently below 0.1 ppm will often improve textile life and colour significantly, which is one reason why some plants operate with very low textile injections into the circulating stock. Iron can still be a big problem in large areas of London and occurs locally in many others worldwide. Cruise liners filling their tanks at different ports of call or using desalination have had to learn to cope with widely varying iron levels.
- Cleanroom water must also be free of bacteria and particulates, which may call for microfiltration or disinfection using UV rays or other methods, coupled with the monitoring checks needed (best provided by the engineer). Simple and inexpensive checks made in-house are now possible, with brief training available.
- Steam supply into the laundry has traditionally been from a central boiler burning fossil fuel, but in most plants, this should now be seen as wasteful (20% of the energy liberated goes to the boiler flue) and obsolete (burning fossil fuels will shortly be banned in most regions to limit CO2 emission). In the short term, gas fired dryers reduce tumbler energy costs and CO2 emissions significantly (by 20–30%), which gives immediate, short-term savings.
Laundries which still have a central steam boiler should consider the benefits of eliminating this, to reap the benefits of distributed energy supply. In the short term this would probably involve a correctly sized, natural gas-fired steam generator for the small amounts of steam needed for low temperature washing and the initial steam blast into the tunnel finisher. If trials already under way in the UK are successful, there could be a short-term interim transition from natural gas to a blend of this with 20% hydrogen (which could use the existing national gas distribution networks with only minor changes to burners). This could give an overnight reduction of 20% in the present considerable CO2 emissions from gas combustion, whilst long term measures are trialled and installed.
These could well be based on combustion of green hydrogen (generated by the electrolysis of water using green power from wind, tidal or solar). The chemistry of this is well known and practised, but considerable economies of scale would be needed to make this economically viable. Even so, laundries will need to be ruthless in their energy management and engineers should be developing plans for their own laundries now. We need to be moving from a typical current target for unit energy consumption of 1.0 kWh/kg dry textiles down towards an achievable 0.7 – 0.8 kWh/ kg. LCN will be looking, in the coming months, at techniques to deliver this.
Many healthcare laundries have traditionally installed steam dryers powered by 8 to 10-bar steam, to avoid the risk of thermal damage to polycotton blends and reduce the blinding of cage perforations by molten polythene bags. This could be viewed now as uneconomic. A gas-fired dryer can be programmed to give exactly the desired temperature for each classification, will speed towel drying and protect polycottons. If flatwork and garments are all processed through one cold tumbler, leaving the tunnel finisher and ironer (which are much more energy efficient) to do the drying, there will be a further reduction in energy consumption and CO2 emissions. The towels and other full dry work can then be dried in the remaining tumblers. Polythene bags must in future by removed automatically and consistently, either in Sorting or before, and engineers should be working now on schemes to achieve this (instead of working out the best way of drilling out hard plastic from cage perforations). LCN will be shedding further light on this when current research results are published.
In some regions worldwide, direct gasfired ironers, which use the heat directly from the products of gas combustion, are being used successfully, especially for polyester cotton blends (which are usually easier to dry than pure cotton textiles). However, in most regions, gas-firing is used to heat thermal oil, which is far more energy efficient than using steam. Ironers which use direct gas firing, or which burn gas to heat oil, are likely to become obsolete, unless they can be easily converted to run on a carbonfree fuel such as hydrogen. This will require considerable expertise in handling hydrogen safely (because of the explosion risk) and laundries will need to move quickly to acquire the necessary training and experience in their engineering teams. The other popular alternative could rely on electrical heating of thermal oil, but it is too early to state yet which of these will be the more economical. Much depends on the eventual (very low) cost of renewable generation of electric power.
Cost management contributions by the laundry engineer
- Energy management is part of the natural role of the Laundry engineer, who controls many of the energy parameters day to day. This requires both knowledge of what is needed and the discipline to implement this. At present most laundries are still burning fossil fuels to raise steam, so this must be managed effectively (without any significant investment). This means, for example, keeping on top of every steam leak, monitoring steam traps to ensure that they are only passing condensate, checking time at pressure at the membrane press, repairing damaged insulation, optimising spin times at the washer extractors, minimising hot wash dips, avoiding over-drying at the tumblers and so on. There are still laundries with no policy for utilising the flash steam which is released whenever condensate at high pressure travels through a steam trap, even though this represents over 10% of the fuel account in many plants!
- Water is still not being managed effectively in most plants, despite the reducing availability (and escalating cost) of this vital commodity. Wash dips which are even 1cm over the optimum waste large quantities of this resource (and increase fill time, heating time, chemical dosages and associated costs). The worst management is often seen in the rinse dips, which are frequently not minimised, even though all leading detergent suppliers carry the necessary titration equipment. Launderers are wasting millions of cubic metres per year, all for want of a few vital checks. At the tunnel washer, it falls to the laundry engineer to maintain the accuracy of the variable area flowmeters on the fresh soft intake and the recycle into the hot wash zone. These simply need to be cleaned regularly so that they display the correct flow consistently. Many laundries have invested successfully in energy recycling from the hot drain liquors, but these heat exchangers need to be kept clean and free of blockages in order to deliver the potential energy and cost savings.
- High productivity is frequently seen as the consequence of driving operatives to work faster, but the real kings of high output are those who have identified the critical bottlenecks in their operation and painstakingly removed these progressively, one by one. The role of the Laundry engineer in discussing the opportunities and informing the management agenda cannot be overstated. For example, getting the correct sorting conveyor configuration and speeds is critical to efficiency in the sorting room, with the market leaders setting the example, so that unsorted work arrives in front of the sorters correctly presented and spaced out. Sorting should be one easy and smooth, continuous operation, that requires only the minimum of staff, yet all too frequently it varies between hectic action (and plenty of mistakes) and enforced idleness, whilst everyone waits for the next batch!
Assembly of soiled textiles at customers and in transit
The journey taken by soiled textiles starts at the customer’s premises, with transport of soiled flatwork, for example, from hotel room or hospital ward to the central collection point. There are plenty of examples of customer staff using duvet covers, pillowcases or a folded sheet as a bag to be dragged along the corridor, because management has not provided a proper, suitable alternative. The laundry might need to be proactive in sorting this out, rather than leaving customer service staff to moan unsuccessfully to the customer. The laundry engineer might be really useful here, with some simple innovative suggestions. Similarly, assembling soiled work into suitably sized bulk containers for collection also needs to involve minimum effort and avoid associated damage from rips and drips, and could benefit from engineer input. Getting all this right could in some cases halve customer damage and is not always best left to the customer! The main problem continues to be ‘bag-drag’: that is abrasion, slits and holes from rental textiles used as bags to be dragged along corridors and concrete floors, and which must be rapidly eliminated now!
Transit trolley design
Healthcare launderers have led the way in minimising damage to soiled textiles being assembled at customer sites, with purpose designed and built trolleys which are easy to fill and manipulate, and which can be loaded directly onto laundry vehicles for simple transfer. The best use mainly plastic, with weather-proof lids and rounded corners, and little or no metal. They have also succeeded in achieving primary separation of most foul and infective work by customers at the user premises, with colour coding of some form (typically using distinctive red bags for this).
Apart from being purpose designed for ease of handling and use (including loading and off-loading), bespoke trollies for soiled work will need to be capable of economic and automatic disinfection, not only for healthcare work but soon also for hospitality textiles, The recent pandemic has thrown into stark relief the potential role of textiles in pathogen transmission and this aspect of product quality could shortly be a factor in every hospitality contract. The laundry engineer will also need to become familiar with the principles of the European guidelines set out in EN14065:2016 with regard to assured disinfection.
Sorting
Elimination of lifting, bending and stretching in all operations is now an important part of the engineering function, with particular reference to factors such as conveyors and their speed and elevation, lifting aids, the ergonomics in sorting and packing out and so on. Barrows should be seen as largely obsolete in laundries, to be replaced by conveyors at waist height, with some use of pneumatic transfer (especially for garments).
Ventilation and air movement, with particular reference to workroom temperature and humidity, is a vital factor in sorting area design. Simply arranging for fresh air to be blown in the direction of the operatives’ faces is not sufficient; the temperature, humidity and velocity need to be controlled so as to assure comfort.
Infection control, particularly in sorting involves the risk of inhalation of pathogens, as well as control of sharps and minimisation of cuts and punctures. This requires that airborne bacteria are always blown away from sorting operatives, for example and any metal contamination is detected automatically wherever possible.