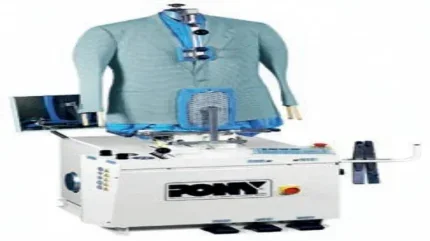
In my experience both ironing table and press clothing are at the lower end of maintenance priorities with few cleaners really understanding the huge contribution soft resilient clothing makes to reducing the time and physical effort needed to produce high quality work.
Types of clothing
There are three basic types of bottom buck clothing available to the cleaner.
- Traditional Clothing: comprises a wire / synthetic gauze, a knitted cotton pad ( KCP ), a felt pad and an outer cover. While this type of clothing initially provides an excellent, resillient pressing surface, it is not as durable as the modern alternatives and if left on the equipment too long KCP’s decompose into a fine brown dust, making their replacement messy and time consuming. I have often seen the cotton canton placed on top of the wire gause with the KCP over thecanton. This can result in faint patterns from the KCP being impressed on fabrics when the vacuum is applied with the head locked, for example on trouser centre leg lays.
- Composite Pads: used on both ironing tables and presses, these are a single structured pad that replaces in one unit the components of traditional clothing. This form of clothing is now thought to be the the most popular, particularly in unit shop operations as it can be quickly replaced. The pads are avaiable in various sizes for use on both presses and ironing tables.
- Silicon Pads: adhesive is normally used to stick the pad to the buck and it is then covered with either a canton flannnel or a siliconised foam pad followed by an outer cover.
Spring tension
Excessive spring tension (often due to incorrect positioning of the springs) causes intermittent soft main creases on trouser legs and waves in the fabric.
Top buck
As for bottom buck ( 1 or 2 ), some alternatives include.
- ‘Fabric Safe‘ ray plates – frequently used on scissor presses dedicated to trouser pressing.
- Wire or synthetic gauze, followed by a canton flannel or silicone foam pad and an outer cover
To avoid premature consolidation it is critical that when press clothing is changed that the locking pressure is carefully adjusted to accommodate the added thickness of the new clothing. (see LCN T. S. July/August 23)
Automated settings
Automated finishers for the most part should be regarded as finishing aids
Recommended steam/air settings
These settings are recommended for rotor cabinets, form finishers and stretch formers. Recommended settings:
Steam 10 – 20 seconds
Air 11 – 30 seconds
Ideally the air time should exceed the steam time by around 5 seconds. The lower setings should be used for lightweight items. Where applicable, reduce air volume for lightweight items.
Some equipment and in particulr rotor cabinets have an additional timer that allows a dwell period between steaming and air blowing ( humidification ) this timer should be set at aroumd 6 seconds.